3 Top Warehouse Systems: Unlocking Efficiency from Warehouse Execution Systems (WES), WCS & WMS
In today's complex warehouse environments, understanding the nuances and functionalities of Warehouse Execution Systems (WES), Warehouse Control Systems (WCS), and Warehouse Management Systems (WMS) is essential. Each system plays a unique role in enhancing operational efficiency and has distinct advantages. Lafayette Engineering, with its comprehensive services in warehouse control systems, is ideally positioned to help businesses understand and implement these technologies effectively.
In today's complex warehouse environments, understanding the nuances and functionalities of Warehouse Execution Systems (WES), Warehouse Control Systems (WCS), and Warehouse Management Systems (WMS) is essential. Each system plays a unique role in enhancing operational efficiency and has distinct advantages. Lafayette Engineering, with its comprehensive services in warehouse control systems, is ideally positioned to help businesses understand and implement these technologies effectively.
WES, WCS, and WMS: What Are the Differences?
Warehouse Execution System (WES): WES is designed to manage and optimize real-time warehouse operations. It acts as a conduit between the WMS and WCS, coordinating tasks and resources for material handling and fulfillment processes, thereby enhancing decision-making and operational flows.
Warehouse Control System (WCS): WCS focuses on managing and optimizing the use of automated equipment within a warehouse. It functions as the connective tissue between higher-level systems and physical automation equipment, ensuring efficient execution of tasks and equipment reliability.
Warehouse Management System (WMS): WMS offers a broad scope of management over warehouse operations. It handles everything from inventory management to order processing and labor management, aiming to boost overall efficiency and integrate with other business systems.
Different Purposes of WES, WCS, and WMS
WES: Streamlines real-time operations by coordinating various tasks within the warehouse, optimizing both automated and manual resources.
WCS: Primarily controls physical automation equipment, directing actions like sorting and material movement, crucial for day-to-day operations.
WMS: Manages broader aspects such as inventory levels, shipping logistics, and workforce allocation, essential for strategic business planning.
Benefits of Each System
WES Benefits:
Enhances operational efficiency through optimized task management.
Provides crucial data for informed decision-making.
Increases flexibility and scalability to meet changing operational demands.
WCS Benefits:
Improves the precision and efficiency of material handling equipment.
Offers real-time monitoring and troubleshooting.
Facilitates seamless integration with other technological systems.
WMS Benefits:
Improves inventory accuracy and reduces errors in order fulfillment.
Streamlines order processing, enhancing customer satisfaction.
Offers comprehensive reporting tools for strategic planning and analysis.
FAQs
Q: What are WMS, WES, and WCS?
A: WMS manages comprehensive warehouse operations, WES optimizes real-time task execution, and WCS controls automated equipment.
Q: How do WES, WCS, and WMS integrate?
A: These systems integrate to streamline warehouse operations, with WES serving as the operational brain, WCS managing equipment, and WMS handling overarching management tasks.
Q: Can WES, WCS, and WMS improve ROI?
A: Yes, by optimizing different aspects of warehouse operations, they enhance efficiency, reduce costs, and ultimately improve return on investment.
Q: What's the primary advantage of WCS over WMS?
A: WCS specializes in real-time equipment control, optimizing the use of automated systems and enhancing operational efficiency.
Conclusion
For businesses looking to streamline warehouse operations, understanding and integrating WES, WCS, and WMS is crucial. Lafayette Engineering provides expert services to help businesses harness the power of these systems, optimizing efficiency and boosting profitability.
Featured Product
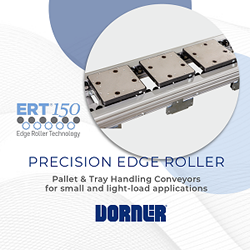