Winder Drive Dimensioning Made Easy With Lenze Drive Solution Designer 4.0
Updated version of drive dimensioning software boasts user enhancements and a specific motion designer for precision dimensioning and drive optimization in winding applications
UXBRIDGE , MA - APRIL 24, 2013 - Leading global manufacturer of electrical and mechanical drives, motion control and automation technology, Lenze Americas has launched an updated version of its Drive Solution Designer (DSD) drive dimensioning tool. Version 4.0 brings DSD users expanded application functionality and enhanced drive dimensioning for winding-unwinding motion control applications.
"DSD 4.0 makes drive dimensioning simpler and even more convenient," states Craig Dahlquist, automation product leader, Lenze. "In addition to numerous user enhancements, the precision drive dimensioning designer for winders offers our customers a powerful new engineering tool."
Lenze DSD 4.0 now comes standard with dimensioning tools for optimizing drives in typical center winding and unwinding machines. The winding-specific motion designer takes into account special features unique to the motion control of winders, with expert support in selecting winding technologies, a diameter-based representation of the load variables, and examination of the winding process in the torque-speed diagram of the motor-inverter combination. The field-tested energy performance certificate, available on earlier DSD versions, completes the winder solution for both single- and multi-axis systems.
Other new features of the Windows-8-compatible DSD 4.0 release include a series of solutions designed for mains voltages in U.S. markets. A new application tuner provides DSD 4.0 users greater detail in precision drive dimensioning and enables varying types of process data to be leveraged in drive optimization. This extended functionality makes it possible to integrate more potential operating states and material recipes into the dimensioning process. Additionally, version 4.0 includes enhancements to usability and improved support for generating CAD data.
"DSD 4.0 incorporates a wealth of process data, motion and speed profiles, and in-depth knowledge about drive physics, variants and energy efficiency applications-automatically calculated and readily available at the user's fingertips-to create a complete, optimized drive structure for all of a machine's motion control requirements," adds Dahlquist.
To learn more about the newly released Drive Solution Designer version 4.0 and other automation solutions from Lenze, please visit www.lenzeamericas.com.
About Lenze Americas
Lenze is a global manufacturer of electrical and mechanical drives, motion control and automation technology. Our products can be found in many industries, including automotive, packaging, material handling and logistics, robotics, and commercial equipment (pumps/fans). A global network of distributors and representatives makes Lenze Americas perfectly positioned to meet the motion control needs of customers worldwide. Lenze Americas, the American subsidiary of Lenze SE of Germany, is headquartered in Uxbridge , Massachusetts ; corporate global headquarters are in Hamelin , Germany . Lenze Americas can be found online at http://www.lenzeamericas.com/.
Featured Product
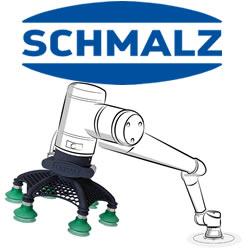