Mondi Selects Metso's Advanced Automation Technology for Ružomberok Mill
With better process control, the mill can improve its overall performance and decrease its environmental footprint
Mondi SCP a.s. has placed an extensive order with Metso for advanced automation technology for its Ružomberok pulp and paper mill in the Slovak Republic. The mill is building a new recovery boiler and a turbine, as well as extending its evaporation plant and lime kiln, which will be run with Metso's automation system. High-tech automation contributes to lower costs, raw material usage, energy consumption and environmental load, while enabling the mill to achieve its targeted quality and performance.
"We chose Metso's solution in order to take advantage of synergies with our existing mill environment, making use of the knowledge of our professionals and operators, as well as minimizing side costs. Another factor that supported our choice of Metso as a supplier was our good experience and cooperation in the past," says Michal Legersky, Project Manager, Mondi SCP a.s.
Metso's scope of delivery will include a complete Metso DNA automation system for the new recovery boiler 3 and the turbine, the evaporation plant and lime kiln extension, as well as for the upgraded operator stations in recovery boiler 2. The delivery also includes application engineering and commissioning. The major part of Metso's automation system will be started up in the fall of 2014.
"The mill already has Metso DNA in all other areas of the recovery island, so the operators are familiar with the system," comments Udo Schober, Area Sales Manager, Automation, Metso.
With production exceeding 474,000 tons of pulp and 535,000 tons of uncoated paper, Mondi SCP is the largest integrated mill producing paper and pulp in the Slovak Republic. Over 77% of its production can be identified as "green" since the energy used for its production comes from biogenic resources while the wood comes from certified, well-managed forests under FSC™ and PEFC schemes. The increased volumes of production thus work synchronized with continuously decreasing the mill's footprint on the environment.
The Automation segment's process automation and flow control solutions meet the growing needs of Metso's customer industries to improve production process efficiency as raw materials and energy sources become scarcer and their costs increase. Our global network of service experts delivers business solutions to our customers that improve their productivity, lower risks and optimize costs.
http://www.metso.com/
Featured Product
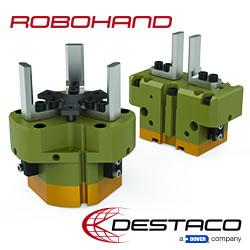