ARES Aims to Provide More Front-line Units with Mission-tailored VTOL Capabilities
Unmanned aerial logistics system would bypass ground-based threats and enable faster, more effective delivery of cargo and other essential services in hard-to-reach areas
U.S. military experience has shown that rugged terrain and threats such as ambushes and Improvised Explosive Devices (IEDs) can make ground-based transportation to and from the front lines a dangerous challenge. Combat outposts require on average 100,000 pounds of material a week, and high elevation and impassable mountain roads often restrict access. Helicopters are one solution, but the supply of available helicopters can't meet the demand for their services, which cover diverse operational needs including resupply, tactical insertion and extraction, and casualty evacuation.
To help overcome these challenges, DARPA unveiled the Transformer (TX) program in 2009. Transformer aimed to develop and demonstrate a prototype system that would provide flexible, terrain-independent transportation for logistics, personnel transport and tactical support missions for small ground units. In 2013, DARPA selected the Aerial Reconfigurable Embedded System (ARES) design concept to move forward.
"Many missions require dedicated vertical take-off and landing (VTOL) assets, but most ground units don't have their own helicopters," said Ashish Bagai, DARPA program manager. "ARES would make organic and versatile VTOL capability available to many more individual units. Our goal is to provide flexible, terrain-independent transportation that avoids ground-based threats, in turn supporting expedited, cost-effective operations and improving the likelihood of mission success."
ARES would center on a VTOL flight module designed to operate as an unmanned aerial vehicle (UAV) capable of transporting a variety of payloads. The flight module would have its own power system, fuel, digital flight controls and remote command-and-control interfaces. Twin tilting ducted fans would provide efficient hovering and landing capabilities in a compact configuration, with rapid conversion to high-speed cruise flight similar to small aircraft. The system could use landing zones half the size typically needed by similarly sized helicopters, enabling it to land in rugged terrain and aboard ships.
It is envisioned that the flight module would travel between its home base and field operations to deliver and retrieve several different types of detachable mission modules, each designed for a specific purpose-cargo pickup and delivery, casualty extraction or airborne intelligence, surveillance, and reconnaissance (ISR) capabilities, for instance. The flight module would have a useful load capability of up to 3,000 pounds, more than 40 percent the takeoff gross weight of the aircraft.
Units could direct the flight modules using apps on their mobile phones or ruggedized tablets. Initially, the system would be unmanned, with a future path towards semi-autonomous flight systems and user interfaces for optionally manned/controlled flight.
ARES is currently in its third and final phase. Lockheed Martin Skunk Works™ is the lead vehicle design and system integration performer for Phase 3 of the program.
Featured Product
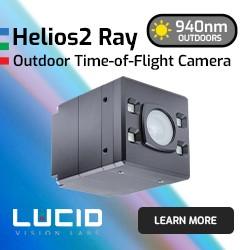