UltraFlex showcasing time- and energy-efficient induction soldering for copper capacitors
Thanks to the digital control of the induction heating parameters, the induction-based soldering would ensure high-quality and repeatable joints.
Staying competitive requires constant pursuit of opportunities for productivity increase and cost optimization. With competitiveness in mind, a company manufacturing electronics components reached out to UltraFlex to increase productivity and reduce the energy costs for their current copper capacitors soldering process.
UltraFlex, being a leading manufacturer of advanced, digitally controlled induction heaters, is willingly setting up test applications for their customers' heating scenarios. The goal of the test applications is to evaluate the heating parameters and time, energy and cost optimizations the customer could achieve by replacing his current heating process with induction-based heating.
For this test application, the customer sent three types of assemblies - pins and pads - to be soldered using induction. The small assembly included a small pad and pin of Ø2 mm, the first big assembly included a small pad and pin of Ø2.5 mm, and the second big assembly had a big pad and pin of Ø2.5 mm. All pads were placed on a plastic base and hence, the heating temperature had to be kept low, to avoid melting the base. The heating had to be done for 3 assemblies from each type simultaneously, to ensure high productivity. Soldering flux with a melting temperature of 185 °C had to be used.
For this heating scenario UltraFlex engineers used induction equipment from the UltraFlex UltraHeat SM series. UltraHeat SM are compact and easy-to-use 5kW induction heaters. They feature adaptive digital phase control providing efficient operation in a wide frequency range.
UltraFlex engineers performed induction soldering tests for each assembly type that was provided. At power output between 4.3 and 4.5 kW, and the same lab induction coil used, it took 16 to 18 seconds to solder the small assembly and the first big assembly. The 3rd, biggest assembly, took a bit more time due to the non-uniform heating of the joints.
After analyzing the results from the test applications, UltraFlex engineers concluded that a custom induction coil could vastly optimize this induction soldering process. It would guarantee uniform heating that would ensure all customer assemblies could be soldered within the desired time. Shorter heating time would translate into increased productivity, as well as into cost- and energy-efficiency of the heating process. Finally, the shorter heating cycles would not allow for the plastic base to melt.
Thanks to the digital control of the induction heating parameters, the induction-based soldering would ensure high-quality and repeatable joints. Finally, this soldering process would be safe and green, ensuring a quality working environment and complete safety for the operator.
Find out more at:
https://ultraflexpower.com/
Contact us at:
+1.631.467.6814
uptnews@ultraflexpower.com
Featured Product
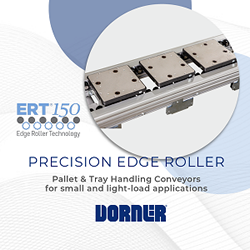
The ERT150 - Dorner's Next Evolution of Edge Roller Technology Conveyors
The next evolution in Dorner's Edge Roller Technology conveyor platform, the ERT®150, is ideal for small and light-load assembly automation, as well as medical and medical-device assembly application. The ERT platform is the only pallet conveyor of its kind available with an ISO Standard Class 4 rating for cleanroom applications. Earning the ISO Standard 14644-1 Class 4 rating means Dorner's ERT150 will conform and not contribute to the contamination of cleanrooms to those standards. As implied by its name, the ERT150 (Edge Roller Technology) uses rollers to move pallets through the conveyor smoothly with no friction (a byproduct often seen in belt-driven platforms). The conveyor's open design eliminates concerns of small parts or screws dropping into rollers and causing conveyor damage or jamming. The ERT150 is suited to operate in cleanroom environments requiring a pallet handling conveyor. It is capable of zoning for no or low-back pressure accumulation and is ideal for automation assembly applications within industries including medical devices, electronics, consumer goods among others.