Air-driven ejectors are gaining pace as the vacuum source for suction cup handling equipment on robots and special purpose machines (ex: case/carton erectors, de-stackers, unloading equipment, etc.)
Contributed by | Piab USA Inc
Introduction
Air-driven ejectors are gaining pace as the vacuum source for suction cup handling equipment on robots and special purpose machines (ex: case/carton erectors, de-stackers, unloading equipment, etc.). It is an ongoing trend in many different industries, such as packaging, electronics, automotive, glass and plastics. The advantages over traditional blowers and rotary vane vacuum pumps are striking; higher reliability, lower investment cost, lower cost for energy and ownership, easier control, easier installation, lower size and weight, are just a few to mention.
The market for air-driven ejectors is flooded with several “all in one” ejectors promising added value through compact lightweight design, intelligent integrated functions, energy efficiency, sophisticated diagnostics/monitor features, etc. For an engineer, designing a robot gripper tool, it is not trivial to select the right ejector package in the jungle of choices. What is really important to consider when selecting the ejector? Which factors make a big difference in achieving a high degree of reliability (uptime) and productivity from the robot system or machine you are designing?
Ex. All-in-one ejector package
This whitepaper will help you better understand the important factors and make your choice easier.
Several special functions can easily hide the essence
The essence of important functions provided on an ejector can be summarized in three major categories.
- Functions to enhance uptime/reliability
- Functions to improve speed/picks per minute
- Functions to reduce energy consumption
Uptime
Most machine builders and robot integrators would agree that reliability of critical components in a machine/robot has great impact in creating a successful and profitable business. A nightmare is critical components repeatedly failing on the machine or robot, creating downtime and upsetting end-customers in production plants, quite often remotely placed and expensive to visit. An ejector unit is definitely a critical component for a suction cup handling systems.
Vacuum ejectors are critical components to guarantee robot/machine uptime in handling systems!
Picks per minute
Besides uptime, machine or robot performance (quite often measured in “picks per minute”), is one of the main parameters that the end-user will measure and judge after installation. The performance of a vacuum handling system depends on the total system solution where ejectors, suction cups and accessories are included. However, one can safely say that the ejector plays a crucial role.
High speed robots and machines need ultra-fast ejectors
Energy consumption
A third area that begins to play an important role for end-users when they select new machines or robots to their plants is energy usage. Several plants have stringent requirements to reduce energy consumption year by year and that adds pressure on machine builders and robot integrators as well. The new ISO 50001 - energy management standard - is growing fast around the world and adds pressure to reduce energy. As mentioned earlier, ejector technology is an efficient way to create vacuum if used and controlled in the right way. However, a poor ejector nozzle design and inefficient part release function, can easily consume 3-4 times more energy compared to the best in class.
So, when selecting an ejector solution, one should pay extra attention to features supporting reliability, speed and energy.
Just like many other industrial and commercial products, ejectors today are loaded with features. Some features will contribute with added value, but several features will not and in reality provide no added value, only a risk of hiding the true performance.
This is an example of an integrated function that one could be skeptical of concerning true added value:
Integrated fixed pressure regulator
An integrated conventional pressure regulator set on a fix value, for instance 3.5 bar [50 psi], will provide very little added value. Normally regulators are used in the machine/equipment for other pneumatic components anyways and it is cheaper to supply several ejectors from a centralized regulator. A correctly designed and efficient ejector nozzle will provide good performance in a pressure range around the optimized pressure making an integrated fixed regulator redundant. With more moving parts integrated, the MTBF (Mean Time Before Failure) will decrease and service/maintenance becomes more time-consuming.
An air pressure regulator, serving several ejectors is probably a smarter choice than integrated on each unit.
Features and functions with true added value
Ejector efficiency – Probably the most important factor. The speed (cycle time) will very much be determined by how fast the ejector can generate a safe vacuum level. If handling leaking materials with material variations (ex. corrugated cardboard) the flow capacity at deeper vacuum levels is equally important to maintaining a high reliability. Initial flow capacity is extra important in high speed machines to secure a tight quick grip with a bellows cup. Multistage ejector technology is 30-50% more efficient as compared to corresponding single stage ejector technology with the same energy consumption. The only “trade-off” with multistage is a slightly longer ejector module. Using a single stage ejector, one must compensate with a larger ejector nozzle to achieve the same performance. That will “cost” in energy consumption, noise level, larger valves, more heat, etc.
Vacuum flow at different vacuum levels divided by air consumption will show the true efficiency of en ejector
Ejector characteristics – The ejector nozzles can be designed for different purposes. To provide extra flow, but lower vacuum levels (good when handling leaking materials), to provide extra deep vacuum levels or to provide a good vacuum performance over a large supply pressure range. From a performance point of view (speed and energy efficiency) it can make a big difference to select the right characteristic for the application. High altitude, >1000-1500m [3000-5000 ft.], is another factor that influences performance of an ejector. A special nozzle characteristic is needed to achieve system reliability and performance at high altitudes.
Blow-off/release efficiency – Almost as important as generating vacuum is to release the object as fast as possible, be as reliable as possible (meaning that vacuum in all cups shall break at the same time) and be as efficient as possible, i.e. using as little compressed air as possible. In some applications (sealed materials) where Energy Saving function (ES) can be used on the ejector, blow-off air typically counts for most of the air consumed in the cycle.
Valve construction and response time – For high speed applications, ex.: cycle times <50- 100ms, the speed of the valves has a big impact on the total cycle time. Direct operating valves will eliminate extra volume for air fill to pilot valves (typically poppet style). Direct operating valves improves MTBF (Mean Time Before Failure) since fewer moving parts is involved in the total valve construction. The power of the valve also determines the speed.
Heat from valves and adaptive PWM – An issue with high power DC valves is heat generation. Heat will reduce the life-span of valves and surrounding components. By using PWM (Pulse Width Modulation) on a DC valve, it is possible to use less power when the valve is holding and only increase power when needed to change position for a few ms. PWM can reduce power and heat generation from valves by > 50%. However, there is a reliability risk with linear PWM technology. If the incoming voltage is very low, the holding voltage could end up too low and valve can change position uncontrolled. This can be avoided with “adaptive PWM” technology. The incoming voltage is measured and the adaptive PWM makes sure holding voltage is always on same level.
PWM (Pulse Width Modulation) - An average value of voltage supplied to the load is controlled by turning the switch between supply and load on and off at a fast pace. The longer the switch is on compared to the off periods, the higher is the power supplied to the load.
Allowed supply voltage span – Most valves used on compact style ejectors with integrated controls are specified for 24 VDC power supply with a quite small voltage tolerance. It is not uncommon that end -users have poor control of the loads on the power supply they use. Valves suddenly stop working and their quality is blamed.. However, quite often investigations show that supply voltage in combination with the compressed air pressure had been out of specification. In order to minimize downtime, machine-builders and robot integrators should pay close attention to the allowed supply voltage range when selecting the unit and/or see if there are other features implemented to allow fluctuations in supply voltage. Adaptive PWM is a method that allows for supply voltage fluctuations.
Adaptive PWM provides fast valve response with lower energy usage. It is a more robust system with a large voltage-span input range that leads to safer valve shift. Better lifetime with lower overall temperature.
Possibility to place ejector close to point of suction – Vacuum generated as close to the point of suction as possible will always be the most efficient, fastest and most reliable solution. All-in-one ejectors are quite often large in size and relatively heavy. In most situations they are centrally placed and serve several suction cups. Transportation of vacuum in long hoses will create flow losses and volumes to be evacuated. That has to be compensated by a larger ejector. There are all-in-one ejectors available where the control section and ejector section can be divided so that the ejector can be placed direct or very close to suction cup(s). A solution like that will improve picks per minute and picking reliability tremendously.
Graph illustrating how much less energy needed if vacuum pump can be placed close to point of suction
Example: all-in-one ejector where control and ejector sections are separated in order to get closer to point of suction. The solution will improve cycle time and reduce energy consumption.
Possibility to have adequately sized vacuum hose - A common design mistake made by several manufacturers of compact (all-in-one) style ejectors is too small sizes on the vacuum ports. Too small of a poor size will lead to small diameters on the vacuum hoses and that cannot be compensated by a larger ejector. This is one of the main design mistakes and causes a lot of poor systems. An easy test is to start the vacuum ejector with all cups open, the vacuum gauge or digital vacuum meter should not show more than -10 kPa [3 -inHg] for an open system. If so, there are major restrictions affecting performance.
Air saving function with adjustable hysteresis - A very good and effective feature offered by most all-in-one ejector manufacturers is an automatic “Air Saving” function. The function will save a lot of air/energy in suction cup systems for sealed materials (metal, glass, etc.), but can also be used when handling slightly leaking materials. The ejector will stop when a set vacuum level is reached and the vacuum level is monitored. The ejector restarts if the vacuum level drops below the low-end of hysteresis (restart level). Micro leakages exist in all suction cup systems and leakage will increase if a suction cup is worn out. A larger leakage will make the ejector unit stop and restart frequently and that will speed up wear on valves and other internal parts. It can also cause an annoying sound when the ejector goes on and off frequently. More sophisticated ejector units have an adjustable hysteresis for the air saving function. By increasing the hysteresis, the frequency of on/off can be reduced that protects the valves. Really intelligent units will be able to determine the size of the leakage and can automatically turn off the air-saving function in case of a large leakage.
GUI (Graphical User Interface) and settings – “All-in-one” ejectors have a lot of functionality and features integrated, for example valves, vacuum sensor/switch, filters, air saving functions, regulators, etc. Quite often it is required that the customer understands how to make settings on the unit in order to obtain the desired functionality. A mistake in the setting can provide severe consequences. A common example is users are setting the air-saving levels below part-present signal level to the robot/machine. That will, most likely, cause dropped parts and downtime. It is recommended to use all-in-one ejectors which offer “fail- proof” installation and settings, i.e. no possibilities to make a mistake.
Setting part present signal, vacuum level for air-saving function and hysteresis on an all-in-one ejector should be made fail-proof in order to eliminate risk for reduced performance or even dropped parts and downtime.
“Plug-and-Play” Air saving function - Beside possible mistakes during installation and setting with severe consequences, such as dropped parts, it is common that setting the level and hysteresis for the air saving function on all-in-one ejectors are quite complicated. Several users, who had paid for an air-saving function and expected to see reduced air/energy usage, missed out on that due to difficulties with setting the function/feature correctly. An all-in-one ejector should be plug-and-play when it comes to the installation/setting of air-saving functions to guarantee that the user is truly benefiting from the function.
Summary
Important functions provided on an ejector, and in particular all-in-one ejector, can be summarized in three major categories.
- Functions to enhance uptime/reliability
- Functions to improve speed/picks per minute
- Functions to reduce energy consumption
A strong recommendation is to review and test the ejectors with respect to these areas before proceeding with machine or robot specifications.
piCOMPACT™ MICRO is a brand new all-in-one ejector platform from Piab, where main focuses have been component/function reliability and picking speed. It is based on COAX®, the most energy- efficient and eco-friendly ejector technology available on the market. COAX® technology as a vacuum source can be a great help to achieve ISO 50001 –energy management – objectives for users world- wide.
The content & opinions in this article are the author’s and do not necessarily represent the views of RoboticsTomorrow
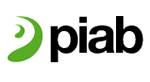
Piab Inc.
Piab provides smart solutions for the automated world, helping thousands of end users and machine producers in e-commerce logistics, food, pharma, automotive and other manufacturing industries to improve energy-efficiency, productivity and working environments. By leveraging the ongoing technological development in automation and robotics, and targeting high-growth segments and geographies, Piab's vision is to become the global leader in gripping and moving solutions.
Other Articles
ProMat Q&A with Piab
Reinventing Intralogistics
The dm Drugstore Distribution Center Relies on Piab Suction Cups
More about Piab Inc.
Comments (0)
This post does not have any comments. Be the first to leave a comment below.
Featured Product
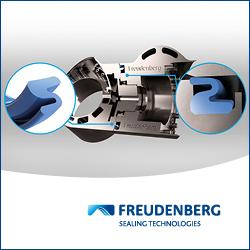