By connecting manufacturing leaders with end-users, implementing machines that are able to maintain themselves and teaching current employees how to work with the new line of industrial robotics, proactive and tech-savvy manufacturers are in a position to revolutionize the way they do business from this point forward.
Why Smart Manufacturing Is Guaranteed to Need Industrial Robotics
Kayla Matthews | Productivity Bytes
Robots are taking the manufacturing industry by storm. This might read like the beginning of the next hugely successful sci-fi novel, but this is the reality within the United States and across the globe. Although many companies have been hesitant to embrace the robotic production line, recent advancements in smart manufacturing are quickly making industrial robotics a necessity in the industry.
Advanced Collaboration
Smart manufacturing takes advantage of the Industrial Internet of Things (IIoT) to achieve greater collaboration between partners, factories, individual production lines and consumers. RFID tags are able to track the movement of materials and goods from their first point of origin all the way to store shelves and, in some cases, right into the household.
Industrial robotics can monitor these smart tags in order to shorten production and shipping times. They can also solicit feedback directly from the consumer regarding product quality and their overall satisfaction. Such information is useful when making future improvements to your manufacturing operations.
You'll also see increased collaboration across the factory floor. Self-diagnosing machines that power down for regular maintenance can save time and money and even prevent injury. A machine in one part of your factory can maintain a real-time connection to a device on the other side of the shop, thereby sharing production metrics or transmitting last-minute production changes. Today's smart equipment can even learn how to increase efficiency over the course of time.
Increased Efficiency
Many human employees are worried industrial robotics will replace them entirely, but the majority of early adopters see the opposite. Instead of replacing your valuable staff members, use this opportunity to give them additional training. Preparing your employees to work alongside industrial robotics is critical when introducing them to the production line.
Automation within the manufacturing industry also leads to greater productivity across the board. Robots are becoming less expensive to implement and manufacturing leaders can use them to improve efficiency in a variety of ways. Not only can they minimize lead times, but automated production robots can be a huge factor in whether or not you meet any tight production deadlines.
Greater Customization
The 21st century has brought about an increased demand for customized projects. Budding entrepreneurs, up-and-coming millennials and even established companies seem to be full of new ideas and innovations as of late. With so many opportunities to get involved and so much potential to tap into, manufacturers would be doing themselves — as well as their customers — a disservice by ignoring smart manufacturing and industrial robotics.
Frank Piller, co-founder of the MIT Smart Customization Group, explained how manufacturing leaders can use this next-gen technology to better meet the needs of individual customers. He cites the IIoT and its capacity for real-time data collection as well as the lower costs and increased availability of raw materials as the driving factors behind manufacturers' increased focus on the consumer.
Despite growing popularity, only 10% of potential manufacturers are currently utilizing industrial robotics in their own operations. This is due to several reasons, including the lack of any standardized performance or usability benchmarks. Such information will likely become available as more manufacturers embrace the new technology.
Reaching Beyond the Limits of Traditional Manufacturing
There are a plethora of brand-new horizons waiting for those who are willing to take a chance on the emergence of the IIoT and smart manufacturing. By connecting manufacturing leaders with end-users, implementing machines that are able to maintain themselves and teaching current employees how to work with the new line of industrial robotics, proactive and tech-savvy manufacturers are in a position to revolutionize the way they do business from this point forward.
About Kayla Matthews
Kayla Matthews is a writer interested in connected technologies, robotics and artificial intelligence. You can follow Kayla on her personal tech blog to read more of her latest posts.
The content & opinions in this article are the author’s and do not necessarily represent the views of RoboticsTomorrow
Comments (0)
This post does not have any comments. Be the first to leave a comment below.
Featured Product
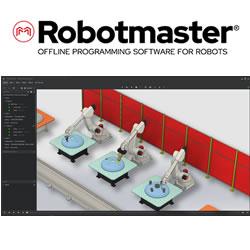