This technology has the potential to minimise those risks by performing a key part of the operation with accuracy which cannot be achieved by a human hand.
Robots to Perform Spinal Surgery With Pinpoint Accuracy
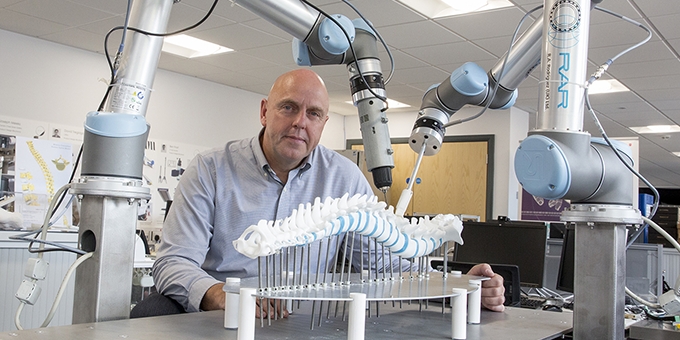
Contributed by | Nottingham Trent University
Robots will perform spinal surgery with greater accuracy than humanly possible as part of a ground-breaking research project led by Nottingham Trent University.
A team led by Professor Philip Breedon, of the Medical Design Research Group, have created a system which allows two robotic arms to semi-autonomously drill holes in individual vertebrae.
The drilling is required as part of an operation which allows surgeons to straighten the spines of patients who have conditions such as scoliosis or kyphosis.
The technology promises to deliver previously unachieved levels of accuracy, partly because the robotic arms move in unison and naturally with the patient’s spine during the operation whilst drilling.
The research also explores the use of augmented reality to provide surgeons with live visual feedback to illustrate the depth of each hole as it is drilled. Accuracy of drilling has been recorded at 0.1 of a millimetre.
“Surgeons performing life-changing operations to correct spinal conditions such as scoliosis or kyphosis have to ensure pinpoint levels of accuracy are achieved to avoid causing unnecessary and potentially serious injuries,” said Professor Breedon.
“This technology promises to deliver greater levels of accuracy than ever previously achieved – or even humanly possible – to improve the safety and efficiency of such procedures which are needed by people with serious spinal conditions.”
The holes drilled in the vertebrae are used to insert pedicle screws which are attached to deformity rod reducers that allow surgeons to lever individual vertebrae and realign the spine.
Two robotic arms work in collaboration during the procedure, known as the datum and tooling robots. The datum robot is secured to a vertebrae and moves with it to follow the natural movements of the patient. It relays data on this movement instantaneously to a computer.
The tooling robot then adjusts automatically so that it remains on its pre-defined path and continues to drill accurately.
It has been undertaken in collaboration with Professor David Brown of Nottingham Trent University’s School of Science and Technology and consultant spinal surgeon Professor Bronek Boszczyk, Head of Spinal Surgery at Benedictus Krankenhaus Tutzing, Germany, and a visiting professor at Nottingham Trent University.
Professor Boszczyk said: “It is paramount that spinal procedures are carried out with total accuracy in order to minimise what can be substantial risks to a patient.
“This technology has the potential to minimise those risks by performing a key part of the operation with accuracy which cannot be achieved by a human hand.
“It's a brilliant example of how robotics can enhance and improve the way in which intrusive operations are carried out, improving patient safety and ensuring efficiency of process.”
The content & opinions in this article are the author’s and do not necessarily represent the views of RoboticsTomorrow
Comments (0)
This post does not have any comments. Be the first to leave a comment below.
Featured Product
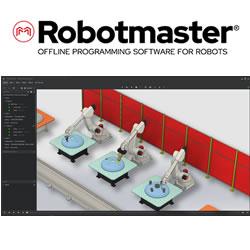