If robots are to solve the labor shortage in US manufacturing, then they will need to significantly expand the type of tasks that they can carry out.
Why Robots Are a Cure Rather Than a Curse for Manufacturing
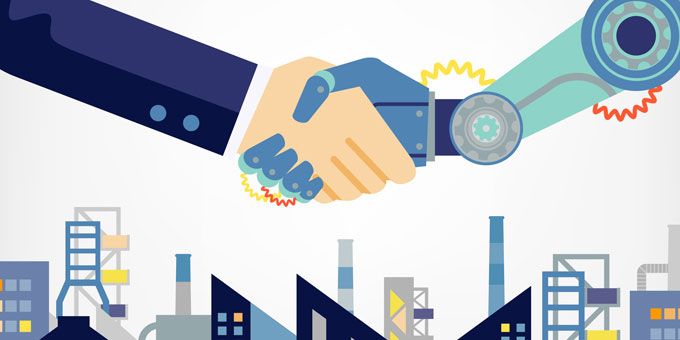
Jason Barton, CCO | Realtime Robotics
You can't escape the fear-mongering around automation, with many claiming that robots will take people's jobs. However, for some industries such as manufacturing, robots can help address the growing labor shortage. Currently, there are over 522,000 available manufacturing jobs in the United States, which is an all-time high. This trend is set to continue with Deloitte predicting that this figure could soar upwards to 2.4 million by 2028. So, automation, rather than being seen as a curse, will be a necessary cure.
The role of robots in manufacturing is still relatively limited and has not fundamentally changed since their initial deployment. Robots remain behind cages and require a vast amount of time and money to integrate them. Simple processes at the beginning or end of the production line are where robots have made inroads to date. For example, with automobile assembly, robots are currently programmed to perform the same operations repeatedly on parts that are always in the same position and orientation.
If robots are to solve the labor shortage in US manufacturing, then they will need to significantly expand the type of tasks that they can carry out. They will need to be a lot smarter than current models so that they can operate safely in close proximity with people and other robots. To expand automation, robots will need to be able to understand and react to unplanned variables at speed. Robots will also need to be more dexterous, have spatial awareness, and the ability to learn.
So how can robotics bridge the manufacturing labor gap?
Robots are constrained currently by safety concerns and are lacking the ability to navigate dynamic, unstructured environments at speed. This is the biggest challenge that must be solved before manufacturers can expand the role of robotic automation and help address the labor gap. In the coming decade, robots will continually take on more mundane tasks that humans traditionally don't want to do. Robots that can recognize, learn, grip, and react quickly will significantly extend automation in manufacturing.
How Robots can make a difference
Below are a couple of the dull, dirty, and dangerous jobs that are difficult to fulfill with people, but are perfect for robots:
Assembly line: Currently, robots are utilized predominantly at the start or end of the production line. Robots are well suited to the repetitive, tedious and labor-intensive nature of lifting, moving, and assembling parts. This type of work puts significant strains and health complications on people as we are not meant to lift heavy loads repeatedly ad nauseam. Robots, however, can take on these tasks with no ill effects. Higher-skilled and more complicated tasks, such as chassis welding, are more difficult to automate due to dexterity and precision varying between parts. Additionally, welding is too bright for cameras, which makes the learning process and programming accuracy much more difficult. As one can imagine this requires series dedication to finance the programming of robots to complete this one task relatedly, let alone the subsequent assemblies on the line. To broaden the scope of robots, they need to be able to mimic the way people work on the assembly line and be able to deal with a more dynamic environment. Moving forward, as technology advances, robots will be able to expand into these complicated tasks.
Material handling: Palletizing is an area where robots have started to make some initial inroads. This is where the machines stack cases of goods or products onto a pallet to replenish stores. Advanced solutions use pairs of robots working together to complete this task, but only if they are far enough apart to avoid collisions. In addition, they are located in a secure area to protect workers. If any irregularities or anomalies happen, such as packaging is too slippery, damaged or missing, then the robots can’t cope. Employees have to use a significant production interruption process to get safe access inside the secured area, reorient the robots and make sure the pallet gets completed. With the rapid growth of e-commerce, robots need to be able to operate at speed, working in close proximity with other robots and people while performing multiple tasks to keep up with production demands. Autonomous forklift trucks are another area where robots are starting to gain a foothold. However, they currently operate at a snail's pace to mitigate the risk of collisions and injury. Until they can operate at full speed, they are not a commercially viable solution.
The future is robotic
Robotic technology must evolve significantly for robots to take on these new tasks. They will need to become much more dexterous, intelligent, and aware of their surroundings. Until this happens, they can't take on the dull, dirty, and dangerous work that humans no longer want to do. Automation is set to transform manufacturing in the coming decades, and it will help address the growing labor gap. Rather than fearing machines, workers and manufacturers should view robotic automation as a cure to a growing problem.
The content & opinions in this article are the author’s and do not necessarily represent the views of RoboticsTomorrow
Comments (0)
This post does not have any comments. Be the first to leave a comment below.
Featured Product
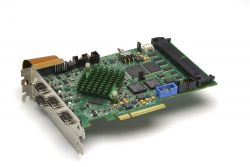