Many applications would benefit from a brushless motor without a sensor. There are various options for realizing this. A method developed by maxon is now setting new standards for precision and reliability.
Sensorless Control of Brushless Motors
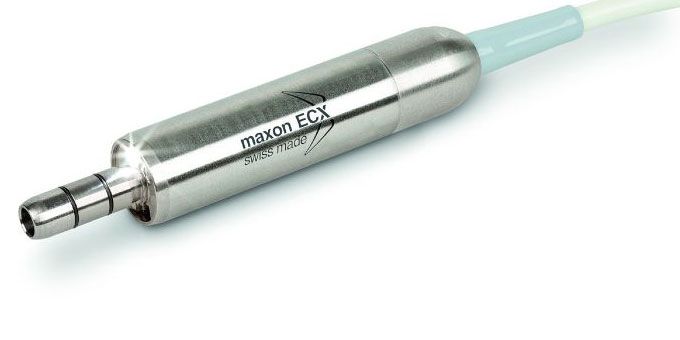
Urs Kafader, Head of Training | maxon Group
Driving a brushless motor requires control electronics for precise commutation. However, this is possible only if the control electronics “know” the exact position of the rotor at all times. Traditionally, this information was provided by sensors, e.g. Hall sensors, installed inside the motor. But it can be done differently. Sensorless control methods use current and voltage information from the motor to determine the rotor position. The motor speed can then be derived from changes in the rotor position, and this information can be used for speed control. More advanced sensorless control methods can even control the current (torque) and the position. Leaving out the sensors has a range of benefits, such a lower cost and space savings, because cables, connectors, and sensitive electronic circuits become unnecessary.
Sensorless controllers by maxon use three basic principles that are adapted specifically to maxon BLDC motors.
Principle 1: EMF method with zero crossing
The EMF method with determination of the zero crossing uses induced voltage (or EMF) in the non-powered phase during block commutation. The zero crossing happens in the middle of the commutation interval (fig. 1). The time delay to the next commutation point can be estimated from the preceding commutation steps.
The EMF method with zero crossing works only when the speed is high enough, because EMF becomes zero at standstill. Starting up the motor requires a special process, similar to step motor control, and must be configured separately. True sensorless commutation is possible only with motor speeds of 500–1000 rpm and up. The commutation step frequency is used for speed control. The limited feedback information puts some constraints on the motor dynamics, although this can be improved by integrating estimation methods into the control algorithm (observer, Kalman filter, etc.). The EMF method with zero crossing also has a range of benefits: It works for all brushless motor models, and it’s robust and cost-effective. The approach is used in many standard products, such as the maxon ESCON Module 50/4 EC-S.
Principle 2: Observer-based EMF method
Observer or model-based EMF methods use information about the motor current to determine rotor position and speed. The model-based approach yields a much higher resolution of the rotor position. This enables sinusoidal commutation (or FOC, field-oriented control), with all its benefits: Higher efficiency, lower heat generation, less vibration and noise. However, the observer-based EMF method also requires a minimum speed of several 100 rpm to function properly.
Principle 3: Magnetic anisotropy methods
Methods based on magnetic anisotropy deduce the rotor position from the motor inductance, which is minimal when the magnetic flows of the rotor and the stator are in parallel in the magnetic return (fig. 2). Measurement is achieved by means of brief current pulses, which do not cause the motor to move. Unlike EMF-based methods, this method also works at standstill or very low speeds, and it permits sinusoidal commutation. The measured signals are highly dependent on the motor type. The rotor position is determined in a model of the motor, which needs to be parameterized and adapted for each motor. Controllers based on magnetic anisotropy are therefore highly specific products – “plug and play” is not an option. The computation effort required for evaluating the rotor position also limits the maximum speed.
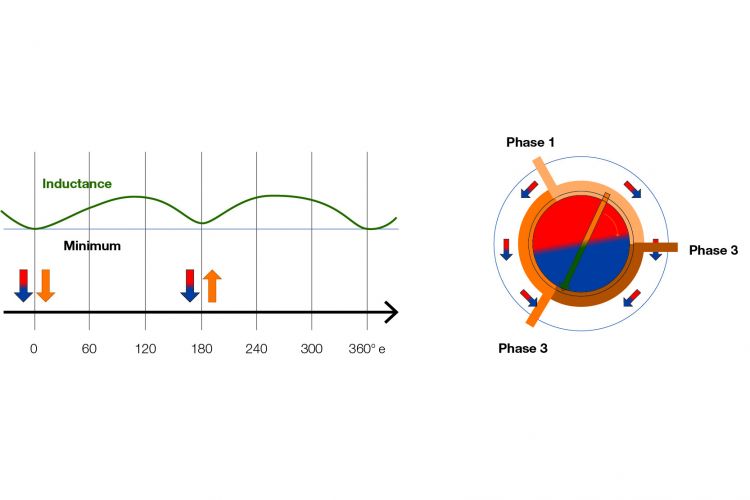
Why sensorless control?
In price-sensitive applications, the use of sensorless motors may reduce the cost. Hall sensors, encoders, cables, and connectors become unnecessary. Typical applications in this field are fans, pumps, scanners, mills, drills, and other fast-turning applications with a relatively modest control performance that do not require a tightly controlled start-up. For high quantities, a customized version of the EMF-based controller makes sense.
Cost optimization for high control performance
Cost savings aren’t the only reason to choose sensorless control. Applications like door drives or bike drives require high controller performance. Jerk-free motor control from zero rpm is important, as are high dynamics and sinusoidal commutation for noise avoidance. All this needs to be realized without using an expensive encoder. Over the last few years, high-quality sensorless controllers based on the anisotropy method have become established, including maxon’s new High Performance Sensorless Control (HPSC, see below). However, the engineering effort required for adapting the model parameters can only be justified for quantities upward of a few hundred.
Rough ambient conditions
Sensorless control may also be required in situations where vulnerable sensor electronics need to be avoided in a motor. Examples include applications in very high or low ambient temperatures, cleaning and sterilization in medical technology, or ionizing radiation in space, nuclear facilities, or medical settings. The lower number of motor connectors also makes integration easier if space is limited.
The required control quality depends on the application. Which sensorless method fits best must be decided on a case by case basis. For example, hand-held dental tools for drilling or grinding need high speeds, while lower speeds and controlled torque are required for fixing screws in surgery.
Conclusion
There are three main reasons for choosing sensorless control: Cost savings, space savings, and operation in environments unfavorable to sensors. The EMF method with zero crossing determination is widespread in cost-sensitive applications that run at high speeds. Sensorless control from standstill and at low speeds requires more advanced methods. The implementation effort is greater and includes modeling and parameterization. Cost savings are secondary. Field-oriented control yields a higher efficiency, less heat build-up, and a lower vibration and noise level. All these are advantages that come to bear especially in hand-held medical devices.
maxon sensorless controllers
The HPSC Module 24/5 (High Performance Sensorless Control) is a new development from maxon, it is a platform of hardware and customer-specific software. HPSC is always a customized solution and therefore not a catalog product. What’s special about this development: At standstill and at low speeds, magnetic anisotropy-based control technology is used first (principle 3). Then, when the speed is higher, a smooth transition to an observer-based EMF method (principle 2) follows. The module’s firmware is customized for every drive system. In a special tuning process, more than 120 parameters are automatically adjusted to each motor’s “fingerprint.” An example of the use of HPSC is the hand-held medical tool developed recently by maxon.
The ESCON Module 50/4 EC-S is the only sensorless controller from maxon that is listed in the product catalog (block commutation with EMF method and zero crossing determination). The Sensorless Controller 24/1 is an alternative for the smallest EC motors (up to about 10 mm diameter). However, it is not listed in the catalog or the e-shop.
The content & opinions in this article are the author’s and do not necessarily represent the views of RoboticsTomorrow
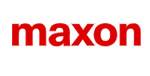
maxon group
maxon is a leading supplier of high-precision DC brush and brushless servo motors and drives. These motors range in size from 4 - 90 mm and are available up to 500 watts. We combine electric motors, gears and DC motor controls into high-precision, intelligent drive systems that can be custom-made to fit the specific needs of customer applications.
Other Articles
Optimizing Material Handling Processes for Increased Efficiency
200 Times Faster Subsea Inspection
Logistics Robots in the Ready-to-wear Fashion
More about maxon group
Comments (0)
This post does not have any comments. Be the first to leave a comment below.
Featured Product
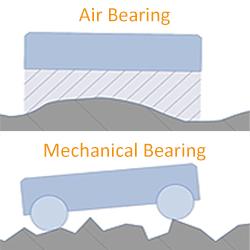