In the search for alternatives to mass products, the industry is increasingly relying on customization. Thus the filling and packaging solutions are also becoming ever faster and more flexible.
Innovative Gripper Solution for Robot-based Handling in Automated Aseptic Filling Processes for Pharmaceuticals
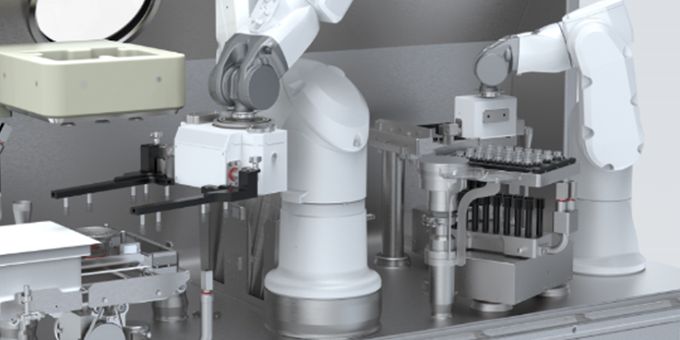
Case Study from | Zimmer Group US, Inc.
The trend toward customization and personalization of mass products is growing rapidly. Having already been observed in automotive and food production, this trend is now also being seen in the pharmaceutical industry. In the search for alternatives to mass products, the industry is increasingly relying on customization. Thus the filling and packaging solutions are also becoming ever faster and more flexible. Small batches, fast product change-overs and customized solutions: More automation, less user intervention and higher availability are in demand. And, of course, the technology of the future should be capable of independently adapting to changing requirements.
In view of production space conditions becoming ever tighter, high labor costs, a shortage of specialists and above all the safety of the operators and of the entire process, the machine manufacturer Bausch+Ströbel has responded to the trend toward more automation and customization by introducing the flexible VarioSys production system. This modular and aseptic production system fully automates the filling and sealing of ampoules, syringes and vials, and it does this flexibly and for small filling amounts. VarioSys combines a standardized cleanroom isolator with a replaceable machine module.
Filling and packaging processes are the specialty of Bausch+Ströbel (B+S). The company is an experienced and competent partner in these processes for the pharmaceutical industry. B+S filling and packaging systems are used worldwide for processing high-quality liquid and powder medications, syringes, vials, cartridges and ampoules, starting with object cleaning and sterilization and going up to labeling and syringe assembly. In addition to developing, engineering and building systems that are specially tailored to the needs of customers, Bausch+Ströbel offers a large range of services—as a competent partner for safe and continuous production at the facilities of our customers.
Recently the VarioSys system from B+S was expanded by a new machine module (DDM 9105) with new functions. Now it enables fully automated opening of tubs as well as fully automated opening, denesting, filling and loading of RTU ("ready-to-use") vials in the nest (packaging unit). The cover film of tubs is detached using a thermal process. For this purpose, they are transported into the corresponding positions by a cleanroom robot, more specifically a gripper. After the tub is opened, a second gripper removes the RTU vials from the nest and hands them to the next module for further processing in bulk. When RTU objects are further processed in the nest, after the tub is opened it is put on a conveyor track to be transferred.
Zimmer gripper for nest handling
For the nest and tub handling of this special application, B+S decided on collaborating with Zimmer Group. One big challenge for the gripper specialist , in addition to perfect interaction with the robot, concerned the use of these grippers in a cleanroom system. Right from the outset this excluded the use of pneumatic grippers—for reasons of space alone, due to the cables and exhaust air. It was decided relatively quickly, therefore, to use a purely mechatronic gripper solution.
On account of the aforementioned challenge posed by the cleanroom, the grippers had to be designed with special consideration for the specifications of technical cleanliness, because they can come into direct contact with syringes and vials and/or with the nest. Commercially available grippers are not immune to particle transfer and unwelcome spreading of particles. Abrasion debris from the gripper itself can produce unwanted foreign objects. This means they present a particular challenge to designers of cleanliness-sensitive systems. As one of the first design measures, therefore, B+S chose easily removable and sealed enclosures or sheathings with a closed surface for the grippers to prevent particles from intruding into the process.
For B+S the flexibility of the grippers was also of critical importance, because the system itself has a very adaptive or modular design and the packaging sizes can change at any time.
As a result, the two grippers best suited to the respective task, GEH6180IL and GEH6040IL, were selected from the extensive Zimmer Group portfolio. Both electric grippers have a large stroke and a servo drive with an integrated controller. The brushless drive technology guarantees not only individual force adjustment, but also control of position and speed. The safety of the system is also an aspect that cannot be neglected, because fragile glass and plastic are handled most. Accordingly, the grippers also have a mechanical self-locking mechanism, which prevents a vial from falling in the event of a power failure.
The fact that Zimmer Group was also able to respond very quickly to necessary modifications (for the GEH6180IL, for example, a lateral connection by means of a flush connector) was particularly appreciated by B+S. They also appreciated the fact that the grippers have only a single cable outlet—that represented a very big advantage for the strictly tight space conditions in the cleanroom. Furthermore, equipping the system with IO-Link made it easy to read out specific data, such as the temperature measurement, position and number of cycles.
Just a few years ago work was done manually
Just a few years ago the tubs were opened and denested manually. For the cleanroom, there used to be an operator employed specifically for doing the nest handling and tub handling work with two glove ports in the module. Today, this production step can be handled using two robots and their grippers with 100% In-process Control (IPC) at full machine output (up to 60 tubs per hour). Thanks to the complete automation, now in addition to cost savings from fewer personnel expenses it is possible above all to increase the process reliability.
"Particularly the ease of configuring parameters and the many additional features of the GEH grippers were very appealing to us," says Philip Messerschmidt and Andreas Höppel, developers at Bausch + Ströbel. “The active and open communication between the Zimmer Group experts and our team characterized our very good collaboration and confirmed our decision to use the Zimmer grippers," adds Lukas Bindewald, Product Manager at B+S. As a result, new potential projects are already being discussed for the future.
Fig. 1: The new machine module of the flexible VarioSys production system for fully automated opening of tubs and for denesting RTU vials
Fig. 2: GEH6000IL gripper from Zimmer Group in use at Bausch+Ströbel
The content & opinions in this article are the author’s and do not necessarily represent the views of RoboticsTomorrow
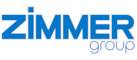
Zimmer Group US, Inc.
Are you interested in premium products in the fields of mechanical and plant engineering? Do you want to learn more about our solutions in the fields of automation, damping, linear, processing, tooling, and machine tooling technology?
Other Articles
Converting Passenger Aircraft to Freight Aircraft - the Zimmer Group Is on Board!
Automated Loading and Unloading of CNC Machines
2021 Top Article - How to Find the Right Damper for Your Application
More about Zimmer Group US, Inc.
Comments (0)
This post does not have any comments. Be the first to leave a comment below.
Featured Product
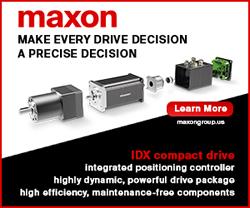