For any Offline Robot Programming solution to be effective, the virtual robot cell set up in the software must be identical to the existing physical robot cell. OCTOPUZ refers to this process as “implementation”.
Is your OLRP Implementation Process SMART?
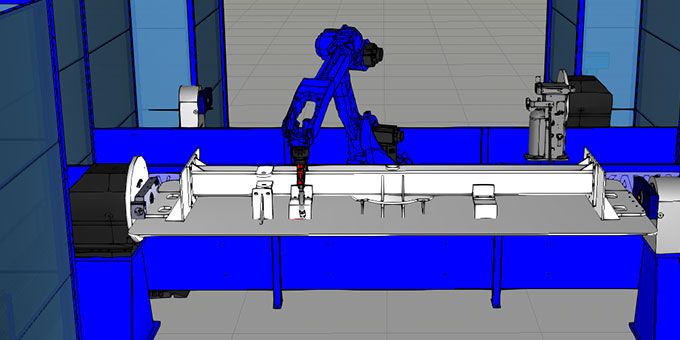
Chris Heit & Brad Patterson, Application Engineering Specialist | Octopuz
What is Implementation & Why is it Important?
For any Offline Robot Programming solution to be effective, the virtual robot cell set up in the software must be identical to the existing physical robot cell. OCTOPUZ refers to this process as “implementation”, but other industry terms include “virtual calibration” or “software commissioning”. Implementation consists of two critical phases: Component Alignment and Robot Code Generation:
Component Alignment:
The components in the virtual cell must be aligned to match the locations of the components in the physical cell relative to the robot(s) in the cell. This ensures that programs, paths, and points that are exported from the OLRP software to the physical robot cell drive the robot(s) to the correct locations and produce quality parts. This is usually done by mapping out and measuring the locations of the physical components and bringing those measurements into the OLRP software. This measurement is often done using the robot itself to produce the best alignment relative to the robot.
Robot Code Generation:
The post-processors are the scripts that translate the simulation into robot code. They must be configured such that the robot programs they generate will load and run on the physical system without error. This process can be accomplished using a variety of methods. Typically, all methods result in comparing the code structure (syntax) of the real system with the OLRP generated code and ensuring they are identical. This is important as each robot system may have a special setup or syntax that requires some custom functions to be included in the generated code.
What Does SMART Implementation Mean?
The phases described above sound simple but are often complex for those experiencing OLRP for the first time. To navigate and address these complexities, OCTOPUZ has developed the SMART Implementation process. During SMART Implementation, a digital twin is created allowing users to program their robotic applications using OLRP, then generate robot-specific code to be run on the real system. This process consists of five unique steps: Survey, Measure, Align, Repeat, and Test. The SMART process ensures that all components and alignments are properly calibrated and tested.
This service is offered in two formats (onsite or remote) to serve our customers in whichever way is more efficient for their timeline.
Survey:
The first step is to identify all components in the real system that will need to be calibrated and located to have an accurate representation of the cell in OCTOPUZ. This includes robots, externals, stationary objects, and any other components necessary based on the cell setup. Once an evaluation of the cell has been completed, the process of recording measurements can begin.
Measure:
This process involves taking a wide range of points using the real robot to locate all components in the cell relative to the robot itself. As many points as needed are recorded to ensure all inaccuracies and errors are dialed in to ensure the overall accuracy of the OCTOPUZ digital twin. Apart from recording point data, the kinematics of each component is checked to ensure the behavior of the OCTOPUZ model matches that of the real system component.
Align:
Once measurements and kinematics are verified, the point data recorded is imported directly into the OCTOPUZ software. This then begins the iterative process of aligning components with the collected data. Each alignment is followed by a verification program that is loaded on the real system and touched up. The touched-up program points are then imported into the software again and the component alignment is more refined. This process continues until the robot is within an acceptable tolerance.
Repeat:
The process of survey, measure, and align is continued for all components until each component identified is located accurately within the OCTOPUZ cell.
Test:
Our team ensures the system is running as expected using OCTOPUZ generated code before the service is complete. A sample part is typically asked to be provided during the service so the team can create a sample test program that verifies the application calls, the alignment, and code specifics based on the system setup.
What are the Benefits of On-Site Implementation?
When an on-site implementation is possible, an OCTOPUZ Applications Engineer travels to your facility. When on-site, we begin by importing your CAD file(s), robot, and external axes into OCTOPUZ. We then run calibration programs to test and confirm the accuracy of the virtual cell. Once your OCTOPUZ setup is complete and verified, our Applications Engineer conducts on-site training at your facility, so you can confidently navigate the software.
What are the Benefits of Remote Implementation?
Our OCTOPUZ Remote Implementation (ORI) service enables you to calibrate your physical robot systems with the OCTOPUZ software. During your ORI, you have a dedicated OCTOPUZ Application Engineer who will guide you through every step of the calibration process, assist you with any challenges that arise, and ensure your calibration is successful.
Our ORI service is a great option if any of the below is true:
- Travel to your site is restricted or limited.
- Production downtime is limited (minimal access to the robot).
- Your organization has a strong background in robotics (or the system being calibrated).
- There are multiple systems to be calibrated, or there are future plans to make adjustments or add components to the physical system.
Why Does it Work?
Our implementation service is something that we take pride in. Whether it is something complex or simple, we take the time to walk customers through their solutions. We are dedicated to the customer throughout the entire process to ensure all steps are completed successfully and performed accurately.
The content & opinions in this article are the author’s and do not necessarily represent the views of RoboticsTomorrow
Comments (0)
This post does not have any comments. Be the first to leave a comment below.
Featured Product
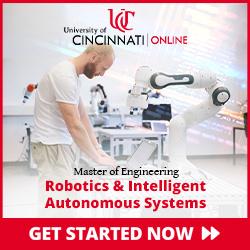