OLRP provides a virtual environment to complete robot programming without taking the robot offline, thereby simplifying complex and time-consuming programming.
Making Robotic Programming Easier for the Fabrication Industry
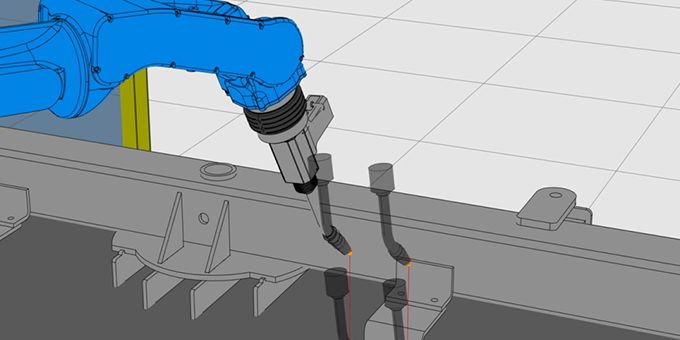
Q&A with | Octopuz
What inspired the next generation of OCTOPUZ software?
Our OCTOPUZ Product Vision is "to enable users to maximize the productivity of their industrial robots by simplifying robot programming." With our vision as our north star, we planned and developed the next generation of OCTOPUZ Offline Robot Programming (OLRP) software by focusing on one key goal:
Create a simplified, intuitive, amazing OLRP experience that keeps industrial robots online and maximizes productivity.
We worked closely with users and partners to define the greatest manufacturing challenges with robot programming and automation and developed solutions that make up our next generation software.
What has changed in this update which programmers can look forward to?
Four key improvements:
A Modern user interface that eliminates complexity and simplifies workflows. We re-designed our platform to provide users with a clean modernized software that is easy to use.
Cell templates that allow users to start programming right away. A cell template is a common environment containing fixed components and other things which don't change between your unique projects or job, such as your robots, positioners, wire feeder, and fences. Every new project - which is your next part to be programmed - begins with a cell template as its starting point so that you can quickly jump in and start programming right away.
Controllers, robots, and positioners connect and interact exactly as they do in the real world. In OCTOPUZ, your robots and positioners all are connected directly to the robot controller. This makes it incredibly easy to program multi-robot systems with multiple rotary and/or rail positioners, all within the same file.
Flexible user-based accounts that let users work from anywhere. To access OCTOPUZ, we've introduced accounts that represent the user. This means that you can log in and program in OCTOPUZ on any computer you like - you're no longer tied to one specific device.
Why would a manufacturer invest in OLRP? How is OCTOPUZ making programming easier for the fabrication industry?
Manufacturers purchase robotic systems to automate jobs that were previously done by humans. Despite the well-documented benefits of automation, robot programming presents its own series of challenges: complex jobs are difficult and time-consuming to program, robot downtime is extremely inefficient due to “online” teach-pendant programming of systems, and it is difficult to find appropriately skilled labour to program robots.
An investment in OLRP solves these challenges by providing a virtual environment to complete robot programming without taking the robot offline, thereby simplifying complex and time-consuming programming, reducing robot downtime, and increasing production efficiency.
OCTOPUZ doubles down on the promise of OLRP by providing simple and intuitive workflows which ensure manufacturing projects are on time and production ready.
Can we expect any more exciting product updates from the OCTOPUZ team this year?
Absolutely. We are investing heavily into our next generation software and are already hard at work on many new and exciting things to simplify robot programming even more.
Manufacturers can stay up to date by checking out What's New in OCTOPUZ.
What types of applications does OCTOPUZ support?
OCTOPUZ enables businesses to do more with their robots by supporting a number of different industrial applications:
- Welding
- Cutting and machining
- Additive
- Spraying
- Factory simulation
About James Schnarr
James Schnarr is the Product Manager of OCTOPUZ software. James' goal is to keep industrial robots online and maximizing productivity by delivering an amazing Offline Robot Programming experience.
The content & opinions in this article are the author’s and do not necessarily represent the views of RoboticsTomorrow
Comments (0)
This post does not have any comments. Be the first to leave a comment below.
Featured Product
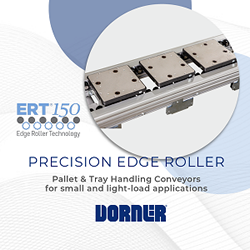