In today’s demanding market, efficiency of operations is an essential factor to remaining competitive. One area where there are often substantial opportunities for improvement is your warehouse pick paths.
Implementing the Most Efficient Picking Paths to Meet Crucial KPIs
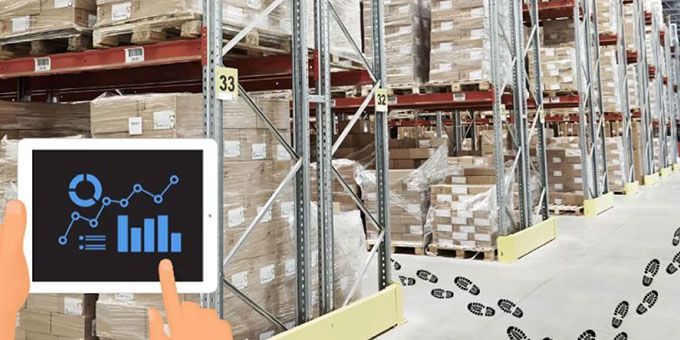
Article from | Hy-Tek Intralogistics
Understanding and optimizing these paths can significantly reduce wasted time and resources, leading to better overall productivity.
Understanding Warehouse Pick Paths
When it comes to warehouse operations, efficiency is key. Every second saved in the order fulfillment process can have a significant impact on overall productivity and customer satisfaction. That’s why understanding and designing efficient pick paths is crucial for warehouse managers.
What is a Pick Path?
In a warehouse, a pick path is the route an associate takes to fulfill a customer or store replenishment order. It’s the literal path they walk or ride, moving from one location to another to “pick” each product needed to complete a given order.
The Importance of Efficient Pick Paths
An inefficient pick path can lead to wasted time and energy. Employees may find themselves backtracking or crisscrossing the warehouse unnecessarily. This not only slows order fulfillment but also sends operational costs soaring.
On the other hand, a well-designed pick path promotes not only speed but also accuracy, as it is easier to ensure that the right products go to the right places. By reducing the chances of picking errors, efficient pick paths contribute to customer satisfaction and minimize returns or exchanges.
It’s important to note that pick paths are not a one-time design. As product assortment, order volume, and warehouse layout change over time, pick paths need to be continuously evaluated and adjusted to maintain optimal efficiency.
Analyzing Your Current Pick Paths & Establishing Baseline Metrics
Before it can be improved, your current pick path efficiency needs to be measured and evaluated to determine a baseline of success.
This includes identifying any inefficiencies and considering how the warehouse’s layout contributes to pick paths.
A pick path could be analyzed by tracking historical data for metrics like ‘average distance traveled to fulfill order’ or ‘picks per hour’.
The picks per hour (pick rate) is determined by dividing the overall number of picks by the total time spent, usually measured in hours. To illustrate, if a picker selects 440 items during an 8-hour shift, their pick rate is calculated as 440 divided by 8, resulting in 55. Consequently, their pick rate stands at 55 items picked per hour.
If these metrics were not historically tracked, consider implementing barcode scanning or RFID tracking to map picking travel.
Without the luxury of historical data, these baseline metrics could also be established by performing time and motion studies.
Look for opportunities for path shortening and reducing double handling.
By tracking metrics such as order fulfillment time, travel distance, and order accuracy, you can identify bottlenecks and areas of improvement.
Remember, the goal is not only to optimize your pick path for current operations but also to anticipate future growth. As your business expands, your pick path strategy should be flexible enough to accommodate increased order volumes and changing customer demands.
The Role of Warehouse Layout in Pick Path Efficiency
Your warehouse layout plays a substantial role in determining pick path efficiency. During a warehouse layout analysis, there 2 crucial factors to consider: “slotting” and the layout of picking aisles.
1. Slotting: The concept of slotting refers to the deliberate arrangement and proximity of physical picking locations within the warehouse.
This involves the meticulous organization of products based on various criteria, such as demand patterns, product size, weight, and storage space requirements.
For instance, frequently picked items should be placed closer to the packing and shipping areas, reducing the time and effort required for order fulfillment.
Additionally, grouping similar products together can streamline picking processes, as it reduces the need for extensive travel within the warehouse.
You can start slotting with these 5 tips.
2. Layout of Picking Aisles: The design and configuration of picking aisles are equally instrumental in determining the efficiency of your picking operation.
Factors to consider here include the length of aisles, the frequency of transverse or center aisles, and the overall layout of shelving and racking systems.
A well-thought-out warehouse layout optimizes the movement of personnel and equipment within the warehouse.
Shorter, well-organized aisles minimize the time required to locate and retrieve products, reducing labor costs and improving order accuracy.
The placement of transverse or center aisles also plays a vital role, as they provide access to different sections of the warehouse. Proper spacing and arrangement of these aisles ensure smooth and unobstructed movement, preventing bottlenecks and congestion.
In combination, these two major aspects of warehouse layout, slotting, and the configuration of picking aisles, have a profound impact on operational efficiency.
Strategies for Optimizing Pick Paths
Optimization of pick paths can be accomplished through several picking strategies. These might include zone picking, batch picking, and wave picking, among others.
1. Zone Picking
Zone picking involves assigning workers to specific areas, or zones, within the warehouse. They are then responsible only for picking items within their assigned zone.
2. Batch Picking
Batch picking involves picking multiple orders simultaneously rather than individually. This strategy can substantially reduce travel time. However, it may require additional time for sorting and organizing the items after they’ve been picked.
3. Wave Picking
Wave picking is a strategy that combines elements of zone and batch picking. Workers are assigned to zones but also pick multiple orders at once. This can provide a compromise between the speed of batch picking and the organization of zone picking.
However, like batch picking, wave picking can require additional time for sorting once the picking is completed. Therefore, it’s best used in specific scenarios or in combination with other strategies.
4. Storing Inventory in Optimal Locations
As mentioned before, optimizing inventory storage involves strategically placing items for efficient retrieval.
This process entails identifying patterns in SKU affinity or frequently picked items that can be stored together, streamlining operations.
So what if I don’t have software to automatically identify optimal storage locations? While advanced slotting software packages can automate these methods, basic slotting can also be done manually.
The Role of Technology in Pick Path Optimization
You can use automated picking systems and picking software to improve pick path efficiency.
Warehouse Management Systems, or WMS, collect and analyze data from your order pickers. It can allow you to easily reconfigure paths in real-time based on new data or changes in customer order patterns.
Here are a few ways that a WMS can optimize your picking routes:
- Data Collection: The software gathers data about the warehouse layout, the locations of products, and the orders to be picked.
- Order Batching: The software groups orders together based on criteria such as product location, order priority, and delivery time.
- Route Optimization: Using advanced algorithms, the software calculates the most efficient path for pickers to follow. It considers factors like the proximity of items to be picked, the layout of the warehouse, and the shortest travel distances.
- Dynamic Updates: In some systems, the software continuously updates the picking paths in real-time as new orders are received or as the warehouse layout changes. This ensures that pickers always follow the most efficient routes.
- Feedback and Learning: Over time, the software can learn from past picking data and adapt its algorithms to further improve efficiency. It takes into account factors like order patterns, picker performance, and seasonal variations.
- Visualization: Some software provides visual aids, like digital maps or pick lists displayed on screens or mobile devices, to guide pickers step-by-step along the optimized paths.
Successful implementation of a WMS can result in real cost savings and increased productivity.
Key Performance Indicators for Pick Path Efficiency
You will need to establish and monitor management metrics, or Key Performance Indicators (KPI), related to your pick paths. These can include:
- Average distance traveled to fulfill an order (the lower, the better)
- Picks per hour (the higher, the better)
- Picking labor hours and cost (the lower, the better)
Monitoring these KPIs can help identify opportunities for improvement and measure the effectiveness of changes you implement.
Continuous Improvement and Regular Review
Efficient pick paths are not a one-and-done effort. Continuous improvement and regular review can help keep your pick paths, and therefore your warehouse operations, as efficient as possible. This will safeguard your bottom line and increase your operational efficiency, allowing your business to stay ahead of the curve.
At the end of the day, achieving maximum efficiency requires a balance of all these factors, with an openness to change and the courage to embrace innovation.
The content & opinions in this article are the author’s and do not necessarily represent the views of RoboticsTomorrow
Comments (0)
This post does not have any comments. Be the first to leave a comment below.
Featured Product
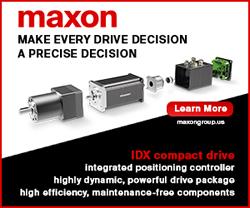