ATX West - A&D Inspection Announces Launch of 600 Gram Checkweigher
The new Checkweigher features a smaller footprint, making the machine easier to integrate into an existing manufacturing process.
Anaheim, Calif. — February 9, 2016 - In In an effort to help a wide range of companies improve their quality assurance and critical control point processes, A&D Inspection announced today its newest Checkweigher - the AD-4961-600-1224 - on display this week at WestPack 2016, Feb. 9-11, in the A&D Inspection Booth (#4911).
The new Checkweigher features a smaller footprint, making the machine easier to integrate into an existing manufacturing process. In addition, the increased product throughput of up to 400 pieces per minute (PPM) makes it that much more efficient. End users will have the ability to increase quality and significantly reduce production costs by safeguarding against underweight and overweight packages.
"The introduction of this new Checkweigher further delivers on our promise of annual enhancements and expansion of our checkweigher and metal detector product lines," Said Terry Duesterhoeft, President and CEO of A&D Company, Americas. "The new product sets the bar for value with a new standard for improved accuracy without sacrificing throughput across a wide range of applications."
A&D Inspections newest Checkweigher features the following key benefits:
• A newly designed digital load cell and an ultra high-speed processing module, allowing it to deliver an unmatched level of precision weighing and measurement at .08g;
• Standard digital inputs and outputs to provide high degrees of user flexibility, allowing for HMI interfacing or the connection of external devices, as well as future expansion to the system;
• A high-visibility touch-panel color LCD screen with a user-friendly interface, including an audio guidance support function;
• Easy upload of product images, to make product identification highly efficient;
• Ability to reach speeds of up to 400 PPM;
• Enhanced protection from dust and water to IP65 standards;
• A modular design, which allows for quick installation or relocation, and simple maintenance; and
• Dual channel airjet rejectors allowing a customer to sort overweight and underweight products.
In all, the AD-4961-600-1224 Checkweigher has four main units, including an in-feed conveyor, a weighing conveyer, a control unit and a base unit for a total system length of just 606 millimeters or 24 inches. Users also do not need to wait for a service engineer to respond to a system shutdown, as they are able to replace any unresponsive modules and significantly reduce potential downtime.
"This new design allows us to serve end users across many different industries that require faster speeds as is common in cosmetics, beverage, canning, and many others," said Daniel Cannistraci, Product Manager for A&D Inspection. "Our customers have yet another option to manage internal quality assurance standards and critical control point issues."
About A&D Inspection:
A business unit of A&D Engineering and part of the A&D Americas family of businesses, A&D Inspection is based in San Jose, Calif. Leveraging A&Ds more than 40 years of experience with technology innovation in the development of precision measurement and control products, A&D Inspection provides quality assurance and critical control points for application in myriad manufacturing industries. For more information on the newest A&D division, please visit http://www.andinspection.com.
Featured Product
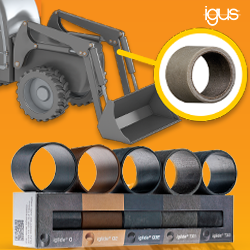
igus® - Free heavy-duty plastic bearings sample box
The iglide® heavy-duty sample box provides a selection of five unique iglide bearings, each suitable for use in heavy-duty equipment due to their self-lubricating, dirt-resistant properties. Each bearing material boasts unique benefits and is best suited for different application conditions, though each can withstand surface pressures of at least 11,603 psi at 68°F.