As this technology is still in its infant stages, we do not truly know how efficient the process will be. We can only hope that the technology will be there when the next spill happens.
Len Calderone for | RoboticsTomorrow
Millions of years ago, algae and plants lived in shallow water, and after they died, they sank to the seafloor, mixing with other sediments. High pressure and temperature, transformed these organisms into oil.
Oil is essential to every segment of our lives, as it is one of the major sources of energy. From oil comes fuel, which is made to run our cars, buses, airplanes and heat our homes, as well as drive our factories. Its components are used to manufacture products, such as plastics, detergents, paints, and even medicines.
Each year, the oil companies remove approximately 3.7 trillion gallons of oil from the earth. This oil is transported by barges, ocean going tankers, and pipelines to refineries and storage facilities. It is inevitable that accidents happen and oil leaks and spills take place. Since oil is mostly transported across vast oceans, the likelihood of an ocean spill is inevitable.
Oil spilled by damaged tankers, pipelines or offshore oil rigs coats everything it touches and becomes an unwelcome part of every ecosystem it enters. Oil spills result in both immediate and long-term environmental damage, and the damage caused can last for decades after the spill.
Oil floats on water spreading out rapidly across the water surface to form a thin layer that we call an oil slick. As the oil continues spreading, the layer becomes thinner and thinner, finally becoming a very thin layer called sheen. When the oil eventually begins to sink into the marine environment, it can have damaging effects on fragile underwater ecosystems. This is where oil eating robots come into play.
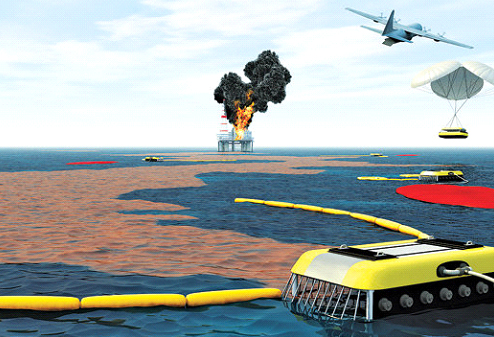
The Global Response Group Corporation’s (GRG) AEROS (Airborne Emergency Response to Oil Spills), is the world’s first and only robotic, unmanned, aircraft-deployed, satellite-guided, oil spill emergency response, rapid containment and recovery system. The AEROS is a fleet of airplane-deployed robots that can contain oil. The airplanes first drop robots and inflatable booms near the spill site. Once inflated, the booms surround the oil and the robots use GPS to get behind the boom’s flap, directing water into the cleaning system.
The robots suck oily water and spin the liquids, sending denser water to the outside and creating a stream of oil in the center. Water that exits the robot is 99 percent pure. Oil collected during the process is stored in bladders, which can later be removed by crew members to recycle. Each robot can cleanse up to 2,000 gallons of oil per minute, scrubbing the oil spill in just a few days.
AEROS is fully robotic, requiring no humans near the water, thus avoiding human contact with toxic vapors and corrosive crude oil. The system works 24/7, and is controlled remotely from aircraft on station or via satellite.
Using conventional methods, less than 5% of the spilled oil is recovered. AEROS can recover up to 90%. The salvaged oil becomes the property of GRG and will be sold to generate additional revenues.
To avoid oil spills around drilling platforms, Liquid Robotics, a start-up in San Francisco, has created a fleet of wave-riding robots for predicting tsunamis, tracking fish, and discovering offshore oil leaks around drilling platforms, possibly preventing rig explosions.
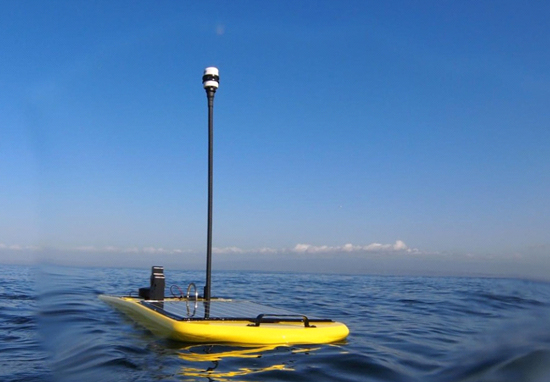
The robots are powered only by the sun and the waves. They are unmanned, and use no fuel, produce no emissions, and travel up to 2,000 miles using only wave power. The robots are covered with solar panels that power on-board scientific instruments along with a GPS. The on-board transmitter uses Iridium satellites to send data to, and receive commands from the company headquarters in Sunnyvale, California.
Because of the need to quickly clean-up oil spills, several new concepts are in the development stage, such as the Protei Project that uses a fleet of robotic sailboats to clean the ocean of spilled oil.
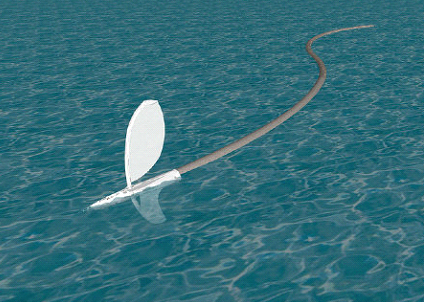
Protei uses the wind to power an unmanned sailing drone, which pulls a long oil-absorbent tail upwind. A fleet of Protei will work as a swarm, or be remotely controlled individually from the shore, using a number of special algorithms in combination with GPS data. The sailing drone will be able to collect up to 2 tons of oil.
Since the sail drones will be remotely controlled, gamers would be employed to increase the effectiveness of the drones. Protei will have the advantage of being unmanned, green, affordable, self-righting and continuously swarm. Protei is being developed as an open standard so anyone can use or modify the design.
You’ve seen the Roomba® run around, cleaning the floors of homes. The Bio-Cleaner system is just a concept at this point, but if the technologies it employs were readily available it would be an invaluable asset to oceanic oil cleanups.
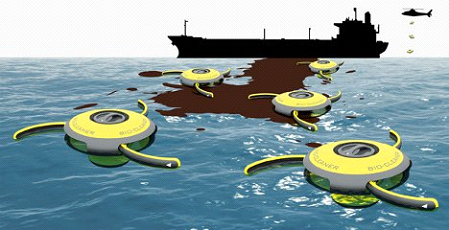
This device floats on the water after being set out from a helicopter or boat. It can track the source of the spill and concentrate on cleaning the spill in that area. In the middle of the robot is a compartment full of oil hungry bacteria. As the oil splashes into the compartment, the bacteria degrade the oil and returns clean ocean water.
Not many fish would investigate the Bio-Cleaner, but there is an acoustic warning mechanism that would warn sea animals away from the danger zone, defending the integrity of the marine food chain.
To clean up future spills, a team at MIT has unveiled their solution: a solar powered, oil-guzzling robot. The robot is 16 feet long and seven feet wide, and uses a nanowire mesh that's able to absorb up to 20 times its own weight in oil. The mesh is run through a conveyor belt-like device that makes up the bulk of the robot and is powered by a large solar panel located on top of the device. The idea is that the robots will form coordinated teams of up to 10,000 units in order to clean up spills as effectively as possible.
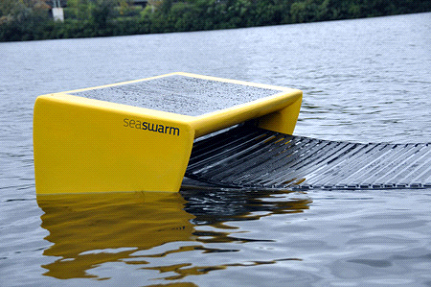
The flexible conveyor belt softly rolls over the ocean’s surface, absorbing oil while deflecting water because of its hydrophobic properties. Each robot communicates its location through GPS and WiFi in order to create an organized system for collection that can work continuously without human support. Because the robots are smaller than commercial skimmers attached to large fishing vessels, they are able to navigate hard to reach places like estuaries and coast lines.
Cleaning oil spills is an expensive proposition. If the spills can be contained as they happen, the cost and the damage to the ecology can be minimized, if eco-friendly robots are quickly deployed to the spill area. The robots can work quickly and efficiently, including deeper penetration to collect more oil. Robots do not have to worry about bad weather as they go about their job.
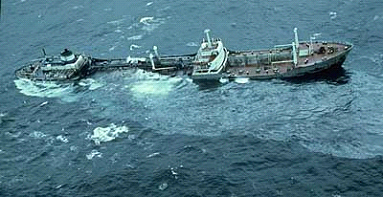
Argo Merchant Spill
Large oil spills like the Deep Water Horizon, Exxon Valdez and the Argo Merchant don’t happen regularly; when they do, the cost and damage to the environment is enormous. The oil companies are not able to stop future spills but they can be prepared to quickly contain the damage. As this technology is still in its infant stages, we do not truly know how efficient the process will be. We can only hope that the technology will be there when the next spill happens.
For additional information:
- http://www.globalresponsegroup.com/ASSETS/SullivanNAICE2009.pdf
- http://www.bmscat.com/oil-spill-response.aspx
- http://www.arctic.gov/publications/oil_spills_2012.pdf
- The implications of the April 2010 oil spill on deepwater exploration and production
- http://www.spill-international.com/whitepaper/index.php
Len has contributed articles to several publications. He also writes opinion editorials for a local newspaper. He is now retired.
The content & opinions in this article are the author’s and do not necessarily represent the views of RoboticsTomorrow
Comments (1)
Len, nice job on the article. The issue may not if we have the robots but will they be accepted. We attempted to put our 6-wheeler in the gulf during the Deepwater spill for shore cleanup. Yes it went real well after dozens of written proposals, phone calls and state Senators jumping, NOWHERE. It seems they were afraid of "rise of the machine", really people a little less Si-Fi in the diet.
Bill
Featured Product
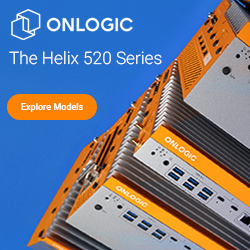
OnLogic's Helix 520 Series of Scalable Fanless Computers
The Helix 520 series utilizes the latest Intel Core Ultra processors with integrated edge AI capabilities to deliver exceptional performance and industrial-grade reliability for demanding applications in automation, robotics, machine vision, and more. Its unique modular design allows for flexible scaling of CPU and GPU performance, while robust connectivity and expansion options ensure seamless integration.