Energid Technologies to Create Robotic Proxy Simulation for Lunar and Planetary Rovers
Digital Simulation Will Support System Development by NASA's Intelligent Robotics Group
CAMBRIDGE, Mass., June 7, 2011 /PRNewswire/ -- Energid Technologies Corporation has been funded by the National Aeronautics and Space Administration (NASA) to develop a proxy digital simulation for lunar and planetary rovers. The Intelligent Robotics Group (IRG) at NASA's Ames Research Center, Moffett Field, California, manages the project.
The IRG at Ames conducts field tests to prepare for lunar and planetary robotic missions, with a field test typically involving 10-20 scientists and controllers, 10-20 operators, and a remote team of 10-20 that travels to a remote location that has terrain matching the needs of the test, usually in a desert.
There is an opportunity in replacing this remote hardware and support team with a digital simulation, or proxy, for some studies. Simulation offers cost savings, a reduced burden on engineers, and improved variation of scenarios for study. NASA has now contracted with Energid to seize this opportunity and develop a proxy simulation.
Two-year funding for this effort follows Energid's demonstration of the viability of simulating a rover and integrating with NASA's tools during a six-month proof-of-concept effort. The approach relies on new modeling algorithms and leverages Energid's existing software.
"This is an ideal application of digital simulation," said James English, Chief Technical Officer at Energid Technologies. "It allows testing environments and situations -- including planetary terrain and operation with teams of robots -- that would otherwise be costly, or even impossible, to reproduce."
The new proxy simulation uses a novel architecture for calculating contact among bodies and modeling interactions. It allows each type of interaction to use a different algorithm, an especially important component.
"There is no universal robotics simulation algorithm," said Chalongrath Pholsiri, Principal Engineer at Energid Technologies. "A wheel rotating against soft soil or regolith responds differently from a metal body striking a rock."
Energid is applying computational methods it developed previously for NASA, the U.S. Department of Defense, and the U.S. National Science Foundation. The development will leverage Energid's Actin™ and Selectin™ commercial robotics software toolkits, which have been used to design, control, and simulate many advanced robotic systems.
"We have many powerful technologies to apply to create the proxy simulation for NASA," said Dr. Pholsiri. "And we will discover more over the next two years."
Work on the project will be done in Massachusetts, Texas, and Arizona. The project is funded through NASA contract NNX11CA22C.
About Energid Technologies
Energid Technologies develops robotic systems and products for the aerospace, agriculture, transportation, defense, and medical industries. Energid's Actin™ and Selectin™ products provide advanced technology in the form of extensible software toolkits. Energid specializes in the sensing, control, and simulation of complex systems.
© 2011 Energid Technologies Corporation. All rights reserved. Actin, Selectin, and the Energid logo are trademarks of Energid Technologies Corporation.
SOURCE Energid Technologies Corporation
Featured Product
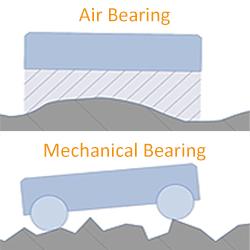
PI USA - Hexapods for 6-Axis Precision Automation
PI Hexapods simplify multi-axis alignment / positioning with a programmable pivot point, tool/work coordinate systems, virtual programming software.