MOTOMAN ROBOTICS INTRODUCES NEW 3D RECOGNITION VISION SOLUTION
MotoSight 3D CortexVision, simplifies the use of 3D vision in robotic guidance applications. This powerful vision solution functions very similar to the human visual process. It is ideal for machine loading, product sortation and welding applications.
MotoSight 3D CortexVision can learn a large number of objects and recognize any of the identified objects regardless of presentation within the visual field of the camera. Within a second, the vision process can identify the part in front of the camera and where it is located. Even complex parts can be identified and then placed accurately.
Minimal downtime is required to train new parts due to its simple point-and-click programming interface. New parts can be trained in seconds, while other systems take minutes or hours to train parts in 3D space. No calibration is required due to advanced algorithm and unique recognition of patterns programmed. Using a single 2D camera (GigE technology), MotoSight 3D CortexVision returns object position information in six degrees of freedom (X, Y, Z, roll, pitch and yaw) without the use of structured lighting. This is an evolutional change in which a single camera can be utilized to provide a 3D solution. Accuracy within +/- 0.5 mm can be achieved with additional inspections.
About Motoman Robotics Division
Founded in 1989, the Motoman Robotics Division of Yaskawa America, Inc. has grown to become the second largest robotics company in the Americas with an installed based of more than 30,000 units. Its products include robotic automation solutions for virtually every industry and robotic application, including arc welding, assembly, coating, dispensing, material handling, material cutting, material removal and spot welding operations.
Featured Product
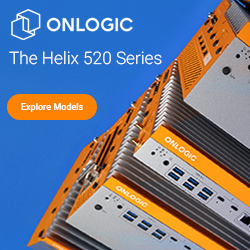