Smart Tether Search and Recovery Technology Using ROVs and SONAR
KCF Technologies has developed a Smart Tether system for Kongsberg-Mesotech sonar units which integrates Smart Tether positioning functionality with the Kongsberg Mesotech MS1000 software.
This system provides a powerful package for quickly performing a comprehensive search of an area and easily documenting the results. KCF has successfully performed lake-bottom scans using this combined system.
With this new capability, it's also quite easy to do ROV-supported scan operations. KCF's test was performed using 2 independently-operating Smart Tether systems, one on the Kongsberg sonar and one on a VideoRay Pro4 ROV. It is very easy to find targets using the sonar and then navigate to them with the ROV, all in real time using the data from the Smart Tethers to coordinate between the two technologies. The ROV can be identified and tracked on the sonar screen as well, providing the ROV pilot additional feedback.
This technology combination can prove very powerful in quickly locating targets and piloting the ROV to them for identification and inspection, allowing an area to be quickly swept without needing to put divers in the water to investigate every target.
Combined with the quick setup time of the Smart Tether, this system allows a very large area to be completely searched and accurately documented very quickly with minimal response time, providing excellent value for first responders and other search and recovery teams.
Featured Product
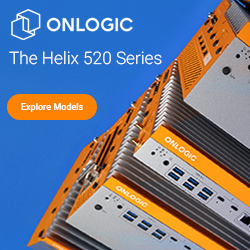
OnLogic's Helix 520 Series of Scalable Fanless Computers
The Helix 520 series utilizes the latest Intel Core Ultra processors with integrated edge AI capabilities to deliver exceptional performance and industrial-grade reliability for demanding applications in automation, robotics, machine vision, and more. Its unique modular design allows for flexible scaling of CPU and GPU performance, while robust connectivity and expansion options ensure seamless integration.