OctoMap 1.2 and updated octomap_mapping stack for diamondback, electric & unstable
Announcement from Armin Hornung of Humanoid Robots Lab, Albert-Ludwigs-Universität Freiburg to ros-users
I'm pleased to announce the release of OctoMap 1.2, along with the updated octomap_mapping ROS stack for diamondback, electric, and unstable (see official octomap page and ROS wiki page). This is major step up from the OctoMap 1.0 release and features many under-the-hood improvements (speedup, leaner code, testing, bug fixes) as well as an improved interface for fellow developers. Key features of the new version are: an adjustable sensor model, node-iterators, time-stamped nodes, and an improved make system. A clean separation of the visualization library means that the octomap_mapping stack no longer depends on Qt or OpenGL (our visualization "octovis" will be released later as an additional ROS package). Furthermore, all output in the octomap package is now using proper ROS log levels (thanks to Eric Perko for the patch).
Changelog - http://octomap.svn.sourceforge.net/viewvc/octomap/tags/v1.2/octomap/CHANGELOG.txt
Download - http://sourceforge.net/projects/octomap/files/octomap-1.2.0.tar.gz/download
ROS packages for diamondback, electric, and unstable are being built and will be available soon. Until then, you can get the `octomap_mapping stack from alufr-ros-pkg (http://code.google.com/p/alufr-ros-pkg/)
Your friendly neighborhood OctoMap team ("Kai and Armin")
Featured Product
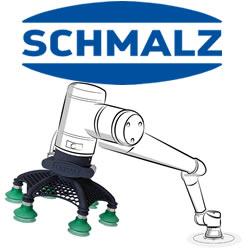