Motoman releases MH80 robot
Motoman releases MH80 robot. The powerful, high-speed MH80 robot has an extremely flexible design, allowing it to be used for a variety of material handling applications.
October 4, 2011 - Motoman releases MH80 robot. The powerful, high-speed MH80 robot has an extremely flexible design, allowing it to be used for a variety of material handling applications. The long reach of the MH80 model makes it ideal for handling large parts. Fast axial speeds and acceleration reduce cycle times and increase production output. Internally routed cables and hoses maximize system reliability, minimize interference and facilitate programming.
The MH80 features an 80 kg (176.4 lb) payload, 2,061 mm (81.1") horizontal reach, 3,578 mm (140.9") vertical reach and ±0.07 mm (0.003") repeatability. Its wide work envelope and small interference zones allow the MH80 to be placed in close proximity to workpieces and equipment, reducing floorspace requirements. The robots have brakes on all axes and can be floor-, wall- or ceiling-mounted for layout flexibility.
In addition to material handling, the MH80 robot is ideal for dispensing and material cutting applications.
The MH80 robot uses Motoman Robotics' DX100 controller that includes multiple robot control technology to easily handle multiple tasks and control up to eight robots (72 axes), I/O devices and communication protocols. Featuring a robust PC architecture with unmatched memory capacity, the DX100 uses a Windows CE programming pendant with color touch screen. The energy-saving DX100 controller features faster processing speeds for smoother interpolation, advanced robot arm motion, built-in collision avoidance, quicker I/O response and accelerated Ethernet communication. Its extensive I/O suite includes integral PLC and HMI pendant displays, 2,048 I/O and a graphical ladder editor that can provide system level control. The DX100 controller supports all major fieldbus networks. It is compliant to ANSI/RIA R15.06-1999 and other relevant ISO and CSA safety standards.
Featured Product
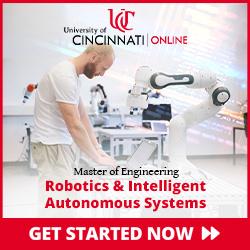