Galil Motion Control Introduces GalilSuite Software Galil Motion Control Introduces GalilSuite Software
Galil Motion Control announced GalilSuite Software Package for configuring, analyzing and tuning Galil motion control systems. GalilSuite has servo tuning capabilities and multiple tuning methods making it easy to automatically tune many types of control systems. The software also allows multiple connections to be made from GalilSuite to multiple controllers.
Galil Motion Control announced GalilSuite Software Package for configuring, analyzing and tuning Galil motion control systems. GalilSuite has servo tuning capabilities and multiple tuning methods making it easy to automatically tune many types of control systems. The software also allows multiple connections to be made from GalilSuite to multiple controllers.
The GalilSuite software package provides five tools for working with Galil controllers:
Terminal - for sending and receiving controller commands
Editor - for writing, saving and executing application programs
Tuner - for selecting controller PID parameters for optimal servo system response
Scope - for plotting controller data such as motor position and velocity
Watch - for displaying controller and I/O status
In GalilSuite each of these tools are independent and can be launched and run individually.
This feature makes it easy for the design engineer to create a flexible development environment for testing control systems.
The Terminal Tool allows Galil commands to be easily sent to and from Galil controllers and provides a Command Helper with Syntax Checker. The Editor Tool allows controller programs to be opened, edited and saved. The enhanced editor is full featured and provides cut, paste, copy, insert and find/replace functions in addition to a syntax helper which includes label detection and syntax help.
The Tuner Tool has many enhancements and provides numerous methods for servo tuning including Crossover, General, Curve Follower and Manual which allows the user to select the optimum method for tuning his system. The user can also select the final test profile as a sine wave, step response, profiled move or custom user code. For each method, the tuner scope captures and displays the controller command position, encoder position, position error and torque in response to the specified test profile.
The Scope Tool is easier to use and has more features than the prior generation. One enhanced feature is that a virtually unlimited number of traces can be displayed such as position, position error, torque, I/O status and amplifier status. The scale for each trace can be adjusted separately along with its position on the scope display. The scope also provides a drag and drop feature allowing easy selection of a parameter from the controller data record by dragging it into the scope display.
The Watch Tool provides an easy-to-read display of various controller data such as controller and amplifier status, I/O and motion parameters. Digital input and output status is shown with virtual LEDs and data such as axis position is shown in numeric format in a table. The update rate of the data capture is selectable.
Featured Product
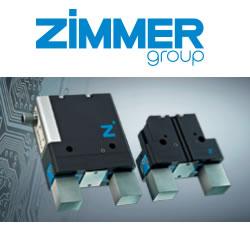