Energid Releases Version 3.0 of the Actin Robot Simulation and Control Software Toolkit
Popular Software Toolkit Enables Powerful Robotic Systems
CAMBRIDGE, Mass., March 2, 2012 /PRNewswire/ -- Energid Technologies Corporation has released version 3.0 of its Actin software toolkit. Actin provides advanced control tools and digital simulation for roboticists.
Robots are growing in capability and economic impact. Much of this growth is driven by faster computer algorithms and software. Energid's Actin toolkit embodies this driving force.
Actin allows roboticists to design complex robots using Computer Aided Design (CAD) programs, quickly build powerful control strategies, then simulate the design's physics and control system in a relevant environment. With Actin, robot design iterations can be made in minutes rather than weeks.
New features in version 3.0 include Graphical User Interface (GUI) design tools with plugin support, grasping and manipulation scripting, tipping control for mobile robots, acceleration filtering and profiling, many new interface devices, more actuator types, advanced configuration using third-party tools, powerful techniques for dynamic collision avoidance, and faster algorithms for simulation and control.
"An example new feature in Actin 3.0 is tipping-prevention control," said David Askey, Chief Business Development Officer at Energid Technologies. "With this control mode, an arm on a mobile robot can be used to automatically keep the center of gravity over the center of the wheels while placing the end effector. This capability makes mobile robots more robust, safe, and effective over rough terrain."
Actin has advanced connections to CAD software. "Energid leverages its Solution Partnership with SolidWorks to enable powerful coupling between the two products," said James Bacon, Principal Software Engineer at Energid. "In addition to traditional joint kinematics and dynamics, SolidWorks can be used to define nontraditional joints, closed kinematic chains, and bounding volumes for collision-avoidance control."
Actin makes new robotics applications possible and fast. In hundreds of robotic systems, in domains ranging from medical applications to oil drilling to planetary exploration, Actin is advancing the state of the art and solving problems. The 3.0 release will accelerate application of the software by increasing the types of problems Actin can solve and decreasing time to market.
"A key to broad application of robotics is easy configuration and tasking," said Neil Tardella, COO at Energid. "Now Energid's customers have just that, through new graphical tools that easily define behaviors. No C++ is required."
About Energid Technologies
Energid Technologies develops robotic systems and products for the aerospace, agriculture, transportation, manufacturing, defense, and medical industries. Energid's Actin™ and Selectin™ products provide advanced technology in the form of extensible software toolkits. Energid specializes in sensing, communications, control, and simulation for complex systems.
Featured Product
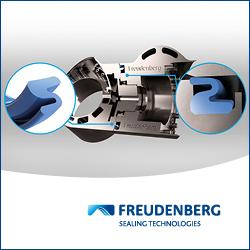
IP Seals for Robots
Freudenberg Sealing Technologies' IPRS (Ingress Protection Seals for Robots) provides reliable protection for robotic systems operating in harsh environments. Designed to prevent dust, moisture, chemicals, and wear from compromising performance, IPRS extends service life and reduces maintenance. The adaptive Z-shaped geometry ensures sealing integrity under continuous motion, making it ideal for high-speed automation and outdoor applications. Manufactured with high-performance elastomers such as Fluoroprene XP and EPDM, IPRS offers exceptional resistance to lubricants, cleaning agents, and extreme temperatures. This makes it the perfect solution for six-axis robots, SCARA robots, AMRs, AGVs, and cobots.
With its low-friction design and durable materials, IPRS enhances energy efficiency and operational reliability in industrial and autonomous robotics. Learn more about our IPRS Seals