Powerful robot coupling for pallet handling
If machine tools are loaded automatically, a reliable, precise, and space saving workpiece change is playing an important role.
If machine tools are loaded automatically, a reliable, precise, and space saving workpiece change is playing an important role. For this particular case, SCHUNK, the competence leader for clamping technology and gripping systems has developed a slim, light-weight coupling with minimized interfering contours, where the pallet loading is taking place very close to the machine table. By using the VERO-S NSR, very thin attachments to the clamping station and pallet are feasible, and therefore a lot of space remains for the workpiece in the machine room, and for the axes motions.
A lightweight handles up to 350 kg
At a weight of 1.6 kg (size 160), the robot coupling achieves pull-down forces of up to 15 kN, and is an extremely rigid system. It transfers torques of up to 1600 Nm, and is also suitable for reliable handling of heavy pallets of up 350 kg (with dimensions of 400 x 400 mm). Every quick-change pallet system of the family-owned company is equipped with a double angle clamping stroke, and therefore allows such high weights. In order to achieve an optimal relationship between rigidity, robustness, and weight, the SCHUNK engineers have designed every part that does not transmit force in aluminum, and parts that do transmit force in hardened stainless steel. The module's locking is self-locking and uses form-fit clamping. At a pneumatic system pressure of 6 bar the module can be unlocked, without needing lubrified air. Opening, closing, and pallet presence are monitored via inductive proximity switches, and therefore the whole changing process can be monitored, too. Moreover, the module with a high compact performance is completely sealed and thus protected against chips and coolant.
Featured Product
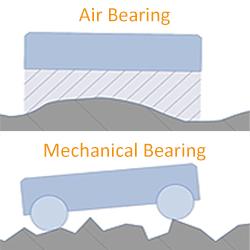