Powerball arm: Maneuverable, powerful and high-precision
The Powerball concept from SCHUNK, the competence leader for clamping technology and gripping systems, takes another step forward: With the fifth generation lightweight arm, the pioneer of modular robotics presents an especially compact and flexible aid for stationary and mobile applications in service robotics and industrial handling.
The Powerball concept from SCHUNK, the competence leader for clamping technology and gripping systems, takes another step forward: With the fifth generation lightweight arm, the pioneer of modular robotics presents an especially compact and flexible aid for stationary and mobile applications in service robotics and industrial handling. The powerful lightweight module from the innovative family-owned company features a weight/payload ratio of 2:1 and is one of the most high-power lightweight arms in the world. At a dead weight of 12 kg, it can dynamically handle loads of up to 6 kg, and has a gripping radius of more than 700 mm. Due to the compact design of the front end, or wrist joint, the arm can be easily maneuvered in close spaces. Its excellent repeat accuracy of 0.06 mm provides for high process stability for demanding measuring and testing tasks. Also, the intelligent design prevents dangerous crushing and shearing movements, making it safe to use around people as well.
Central elements of the lightweight arm are three compact ERB Powerball modules, which combine the movements of two axes. The entire electronic control and regulation circuitry is integrated in the joint drives. Position, speed, and torque can be flexibly regulated. An innovative quick-change system with integrated signal feed-through allows for fast and easy commissioning of the Plug & Performance gripping system. Since the supply lines for gripper and tools are completely within the module, there are no interfering cables on the peripheral devices. Due to the integrated intelligence, universal communication interfaces and cable technology for data transfer and power supply, the arm can be quickly and easily integrated in existing control concepts. The manipulator is supplemented by an industrial robot controller with an integrated CoDeSys PLC. Teaching and instruction is made easy by means of a hand-held control panel with a touch-screen display.
24 V DC supply voltage enables mobile use as well as use at changing locations. Consistent lightweight construction and the state-of-the-art torque motors keep the energy demands of the lightweight arm down to an average of 80 W. That lowers energy costs, provides for longer work periods when using rechargeable batteries, and also allows the use of small-format batteries.
Featured Product
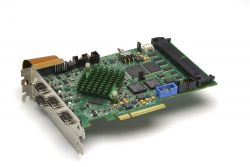