Festo Develops the ExoHand - A Solution for Future Human-Machine Cooperation in Industrial Environments
Festo, a worldwide provider of automation technology, is meeting the challenge of an ageing population with an assistance system that creates a more humane working environment in production and extends people's scope of action.
Happauge, N.Y. April 30, 2012
Presented for the first time at the Hanover Trade Fair 2012, the ExoHand from Festo is a solution for future human-machine cooperation in industrial environments based on soft robotics. It is designed to meet the challenge of an ageing population by functioning as an assistance system for assembly tasks in production. As a force feedback system, the ExoHand can extend people's scope of action in production environments. The system can also be used as a platform for the development of new applications in service robotics as well as personal assistance systems.
Supports various possibilities for gripping and touching
The ExoHand is an exoskeleton that is individually adapted to the human hand. The fingers can be actively moved and their strength amplified. The hand movements can be registered and transmitted to robotic hands in real time. The exoskeleton is a structure that supports the human hand externally and simulates the physiological degrees of freedom of the hand.
Eight pneumatic actuators move the exoskeleton. Sensors record the forces, angles and distances. Servopneumatic open- and closed loop control algorithms allow precise movement of the individual finger joints. The ExoHand thus supports the various possibilities for gripping and touching which a human hand has. The pneumatic components allow highly flexible and ergonomic control of the individual finger joints. High forces can thus be transmitted precisely in a small space and with a low weight without the system becoming rigid and restrictive. This flexibility is crucial in human-machine interaction, as it minimises the risk of injury.
Power boost in assembly
Despite a high level of automation, there are still many assembly tasks in industry that can only be performed by humans. Many of these are repetitive tasks that cause fatigue and can be particularly challenging for older members of the workforce. The ExoHand helps operators to remain working longer without incurring permanent physical damage. It can be used as an assistance system, providing enhanced strength for assembly tasks.
Force feedback - remote manipulation in the industrial environment
When used for remote manipulation of a robotic hand in an industrial environment, the ExoHand allows complex activities in for example dangerous or hazardous environments to be carried out from some distance away. Because all joints and their actuators exist in the form of an exoskeleton outside of the actual hand, the ExoHand can be worn over a human hand or an artificial hand made from silicone. The ExoHand performs two functions here - acting firstly as an interface between the operator and the control system and secondly as a robotic hand. This allows the control of a complete artificial hand with virtually all of the relevant degrees of freedom.
With a single system it is thus possible to design an innovative scenario that combines robotics with orthotics. Forces can be transmitted to the hand as force feedback from another environment, creating an ability to feel shapes. This technology offers enormous potential not only for remote manipulation, but also for navigation in the virtual world.
Synergies in service robotics and rehabilitation
With the ExoHand, Festo has not only developed an effective solution for industrial automation, but also established itself as a pioneer in the area of service robotics. When the ExoHand is used in combination with a robot in domestic or medical environments, human-like characteristics are absolutely essential. The flexibility of pneumatic systems in particular ensures reliable human-machine interaction.
The solution also offers benefits in rehabilitation. In stroke therapy, for example, this hand orthosis can be used to help treat the first signs of paralysis in patients. The ExoHand can be used together with a brain-computer interface to create a closed feedback loop. It can help stroke patients who are showing the first signs of paralysis to restore the missing connection between brain and hand. An electroencephalography signal (EEG) from the brain indicates the patient's desire to open or close the hand. The active hand orthosis then performs the movement. The result is a training effect, which over time helps patients to move their hand again without any technical assistance. Festo is working together with the Centre for Integrative Neuroscience at the University Hospital Tübingen on this subject.
For sales information, call Festo at 800-993-3786 and visit http://www.festo.com/us. Follow us on Facebook, http://www.facebook.com/FestoUSA.
Featured Product
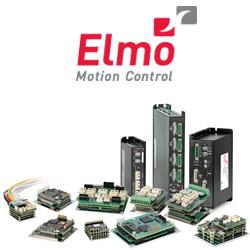
Elmo Motion Control - The Platinum Line, a new era in servo control
Significantly enhanced servo performance, higher EtherCAT networking precision, richer servo operation capabilities, more feedback options, and certified smart Functional Safety. Elmo's industry-leading Platinum line of servo drives provides faster and more enhanced servo performance with wider bandwidth, higher resolutions, and advanced control for better results. Platinum drives offer precise EtherCAT networking, faster cycling, high synchronization, negligible jitters, and near-zero latency. They are fully synchronized to the servo loops and feature-rich feedback support, up to three feedbacks simultaneously (with two absolute encoders working simultaneously). The Platinum Line includes one of the world's smallest Functional Safety, and FSoE-certified servo drives with unique SIL capabilities.