INNOVATIVE CNC HONING MACHINE ACCELERATES PRODUCTION OF PRECISION GEARS
A key requirement of honing automation is that it must have extremely high mechanical rigidity, to ensure accurate and repeatable results.
July 24, 2012 - A high performance 11-axis CNC system from NUM has enabled
new industry standard for post-hardening fine finishing. Using an innovative
honing wheel with external teeth, and an ultra-precise application-specific
CNC program developed by NUM, the Grono 250 machine provides the accuracy of
gear shaving - but in a process that is applied after the gear has been case
hardened - and eliminates the need for shaving and grinding stages.
Sicmat is a leading manufacturer of gear finishing machine tools for the
automotive and automotive supply industries. Until relatively recently, the
company specialized exclusively in machines that used shaving technology to
obtain the necessary finish to gears; this type of finishing process is used
extensively by companies producing medium to high quality gears for the
automotive industry. However, shaving generally has to be performed before
the work piece is case hardened by heat treatment, and any heat-induced
deformation then has to be corrected by grinding or honing. Sicmat therefore
set out to develop a high power honing machine that would help gear
manufacturers accelerate production throughput by reducing the number of
process stages.
Until now, gear honing automation has used highly specialist machine tools,
comprising circular ring type assemblies with teeth cut in their internal
face. These tools are expensive and time-consuming to set up. Sicmat
believed that by using a honing wheel with external teeth, the accuracy of
the process could be improved to such an extent that it could replace gear
shaving in many applications, with the added advantages of lower tooling
costs and much simpler set up. Initial research conducted in collaboration
with the Faculty of Engineering at Turin Polytechnic University - Italy's
top engineering university - proved the practicality of the proposed new
method.
A key requirement of honing automation is that it must have extremely high
mechanical rigidity, to ensure accurate and repeatable results. So, Sicmat
chose to base its new honing machine on the proven mechanical platform of
its RASO TP 250 gear shaving machine. Developed over many years, this
platform has exceptional stiffness and resistance to vibration - its
bedplate is created from electro-welded steel filled with anti-vibration
bonding, and the head, frame and tailstock are manufactured from cast iron.
The platform's physical layout provides excellent accessibility for
operation and maintenance, and its vertical workpiece positioning simplifies
integration with other production line automation.
The Grono 250 has eight motion axes, plus another three on an associated
robotic loader, all controlled by a NUM Flexium CNC system. The motors of
all 11 axes are driven by high power density NUMDrive C servodrives, and the
overall system is equipped with two NUM MDLL 3050 regulated power supplies.
Each power supply is rated at 50 kW continuous and uses regenerative braking
to maximize efficiency. The main machining axes are operated by direct-drive
motors, while the honing wheel and workpiece axes are driven by powerful
high torque motors which are synchronized and controlled by
application-specific software developed by NUM.
According to Marco Battistotti, Director of NUM's Italian facility, the
company's ability to develop custom software was a major factor in Sicmat's
choice of CNC systems provider. "For this application, Sicmat needed
specialist control software to provide extremely tight synchronization of
the machine's honing axes. They also wanted to partner with a CNC company
that was familiar with highly integrated machine architectures and prepared
to handle custom engineering in parallel with their own development efforts,
which are some of NUM's key strengths. The success of our collaboration was
apparent immediately the first machine tests were run; the finished gears
were of exceptionally high quality."
Every stage of the honing process on the Grono 250 machine is automated for
efficiency. In normal use, the case hardened workpiece is removed from the
production line conveyor by a robotic handler/clamp unit, which identifies
the type of gear by checking its outside diameter before transferring it to
an integral pre-process measurement station. Here, the workpiece is
synchronized with a secondary gear, then driven into mesh and rotated
through a complete revolution; during this time, the displacement between
the two axes is measured continuously to ascertain how much stock material
needs to be removed from the workpiece, and this data is fed to the Flexium
CNC system.
After measurement, a further robotic handler transfers the workpiece to the
honing stage, where it is initially indexed before being run up to speed and
synchronized with the abrasive toothed honing wheel. The honing wheel is
then driven progressively into mesh with the workpiece. The two axes operate
in a unique master-slave configuration that has zero delay of the slave
axis, which required NUM to create a second master for the workpiece motor.
Controlling the speeds of both these axes very precisely, and fractionally
varying one relative to the other, facilitates fine adjustment of the honing
process. Current-generation Grono 250 machines are capable of spindle speeds
of 7000 rpm, and Sicmat is already developing a machine with spindle speeds
of 10,000 rpm to provide even tighter process control. As soon as the honing
process is complete, the workpiece is disengaged from the honing wheel, spun
to remove coolant and then transferred back to the production line by the
robotic handler.
Sicmat will be present at this year's International Manufacturing Technology
Show in Chicago. The company's booth is N-6924, where engineers will be
pleased to discuss the unique cost-saving advantages of the Grono 250 gear
honing machine. NUM will also have a large booth - E-5135 - at IMTS 2012,
where the company will be highlighting its expertise in developing custom
CNC software for OEMs and machine builders.
About Sicmat
Sicmat SpA (Stabilimento Industriale Costruzione Macchinario Attrezzature
Torino) was founded in Turin in 1932. The company initially produced
universal machine tools such as radial drilling and shaving machines. In the
early 50s' it moved into more specialist technology involving gear shaping
and chamfering machines for the emergent automotive industry. Sicmat
launched the industry's first shaving machine designed specifically for
numeric control, the RASO 220 CNC, in 1988. Since then, the name RASO has
become synonymous with shaving machines for a large number of gear
manufacturers. Today, Sicmat designs and manufactures a wide range of
technologically advanced machines for gear production, with a particular
emphasis on the automotive sector. www.sicmat.com
Featured Product
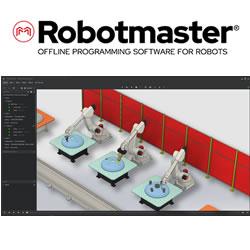
Robotmaster® 2024
Program multi-robot cells and automatically solve robotic errors with ease. Hypertherm Associates announces a new version to its robotic programming software. Robotmaster 2024 addresses key market trends including the support for programming multiple robots in a single work cell and the demand for automatic trajectory optimization and robotic error correction.