Roboteq Launches Revolutionary Sensor for Guiding Robotic Vehicles along Invisible Magnetic Tracks
Its unique sensitivity and accuracy opens a world of new application opportunities
SCOTTSDALE, Ariz.--Roboteq, Inc. (www.roboteq.com) introduces a magnetic guide sensor capable of detecting and reporting the position of a magnetic field along its horizontal axis. The sensor is intended for line following robotic applications, using adhesive magnetic tape to form a track guide on the floor.
The 160mm wide sensor uses advanced signal processing to accurately measure its lateral distance from the center of the track, from a height up to 60mm. With a position resolution of 1mm, the MGS1600 provides the highest precision in the market.
The sensor is primarily used to steer Automatic Guided Vehicles (AGVs), moving material on factory floors. However, its unique sensitivity and accuracy opens a world of new application opportunities, such as automatic shelf replenishing in supermarkets, patient transport in hospitals, stage theater props or rail-less tramways.
Compared to other guiding techniques, magnetic guides are totally passive and therefore easy to lay and modify. The tape creates an invisible field that is immune to dirt and unaffected by lighting conditions. The magnetic track can be totally hidden under any non-ferrous flooring material, such as linoleum, tiles or carpet.
The MGS1600 has a uniquely long list connectivity options: the tape position information can be output in numerical format on the sensor's RS232, USB, CANbus, Analog or PWM ports.
The sensor can be interfaced directly to any of Roboteq's motor controllers in order to create an effective Automatic Guided Vehicle solution with just two components. The sensor can also be connected to any PLC using a choice of Analog, PWM, RS232 or CANbus interfaces. Using USB, the sensor can easily be interfaced to any PC compatible computer.
The sensor will detect and manage up to 2-way forks and can be instructed to follow the left or right track using commands issued via its digital inputs, the Serial, USB or CANbus ports.
In addition to detecting a magnetic guide track to follow, the sensor will detect and report the presence of magnetic markers that may be positioned on the left or right side of the track. Markers are made of the same magnetic tape but of opposite polarity. The markers can be used to signal forks ahead or the presence of a charging station.
The sensor is equipped with several LEDs for easy monitoring and diagnostics. The sensor incorporates a high performance, Basic-like scripting language that allows users to add fully customized functionality to the sensor.
The sensor is delivered with a powerful PC utility for configuring its settings, and updating its firmware in the field with new features as they become available.
To help with system setup and troubleshooting, the utility also includes as a strip chart recorder, and a visualization window to display in real time, the magnetic field as it is seen by the sensor.
The MGS1600 is built onto a compact 25mm L x 160mm W x 20mm H (1" x 4.3" x 0.8") open board module. A fully enclosed, water resistant version will be available in Q2 2013.
The MGS1600 is available now to customers worldwide at $395 in single quantities. Product information and software can be downloaded from the company's web site at www.roboteq.com/sensors/mgs1600-precision-magnetic-track-following-sensor.
A 2 minute video presentation of the MGS1600 can be viewed at: www.youtube.com/watch?v=u_JXSAygeko.
A demonstration robot built by Alliant Technologies (www.atccs.com) using the MGS1600 can be viewed at: http://youtu.be/GDOAkj1GCiQ.
About Roboteq
Founded in 2001 by experts in embedded computing and power electronics, Roboteq's mission is to develop products and technologies that allow novices and professionals alike to build innovative, flexible and affordable mobile robots. Roboteq controllers are now used in over 2,000 original robot designs around the world.
Featured Product
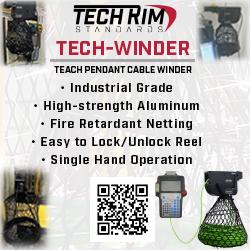
Tech Rim Standards - Tech-Winder Teach Pendant Cable Winder
Tech-Winder is a robust solution for industrial cord management. Aluminum body, for hard impact protection. Flame retardant netting, for added protection against any sparks that may land on the cord. This industrial grade cord reel keeps your pendant cords protected and organized. Stores up to 50 meters (164 ft.) of cable in length with a diameter of 4.5 mm to 10.0 mm. Adapts to NAAMS or Modular Fencing when mounting. Help prevent your next $1,200 factory cable incident, by getting organized with Tech-Winder from Tech Rim Standards.