World's Most Complex 2D Laser Beamsteering Array Demonstrated
New 2-D optical phased array technology to enable advanced LADAR, other defense applications
Most people are familiar with the concept of RADAR. Radio frequency (RF) waves travel through the atmosphere, reflect off of a target, and return to the RADAR system to be processed. The amount of time it takes to return correlates to the object's distance. In recent decades, this technology has been revolutionized by electronically scanned (phased) arrays (ESAs), which transmit the RF waves in a particular direction without mechanical movement. Each emitter varies its phase and amplitude to form a RADAR beam in a particular direction through constructive and destructive interference with other emitters.
Similar to RADAR, laser detection and ranging, or LADAR, scans a field of view to determine distance and other information, but it uses optical beams instead of RF waves. LADAR provides a more detailed level of information that can be used for applications such as rapid 3-D mapping. However, current optical beam steering methods needed for LADAR, most of which are based on simple mechanical rotation, are simply too bulky, slow or inaccurate to meet the full potential of LADAR.
As reported in the current issue of the journal Nature, DARPA researchers have recently demonstrated the most complex 2-D optical phased array ever. The array, which has dimensions of only 576µm x 576µm, roughly the size of the head of a pin, is composed of 4,096 (64 x 64) nanoantennas integrated onto a silicon chip. Key to this breakthrough was developing a design that is scalable to a large number of nanoantennas, developing new microfabrication techniques, and integrating the electronic and photonic components onto a single chip.
"Integrating all the components of an optical phased array into a miniature 2-D chip configuration may lead to new capabilities for sensing and imaging," said Sanjay Raman, program manager for DARPA's Diverse Accessible Heterogeneous Integration (DAHI) program. "By bringing such functionality to a chip-scale form factor, this array can generate high-resolution beam patterns - a capability that researchers have long tried to create with optical phased arrays. This chip is truly an enabling technology for a host of systems and may one day revolutionize LADAR in much the same way that ESAs revolutionized RADAR. Beyond LADAR, this chip may have applications for biomedical imaging, 3D holographic displays and ultra-high-data-rate communications."
This work was supported by funding from DARPA's Short-Range, Wide Field-of-View Extremely agile, Electronically Steered Photonic Emitter (SWEEPER) program under Josh Conway, and the Electronic-Photonic Heterogeneous Integration (E-PHI) thrust of the DAHI program. Future steps include integrating non-silicon laser elements with other photonic components and silicon-based control and processing electronics directly on-chip using E-PHI technologies currently under development.
Featured Product
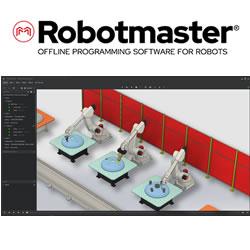