CNC Machining: the Gateway to Robotics
The automated industrial revolution sets a new standard for the marketplace, and Torchmate's computer numerical control is the engine driving robotic technology.
Reno, Nev. April 04, 2013
There is a new industrial revolution in the making, the automated industrial revolution. Computer numerical control (CNC) is the engine that is driving robotic technology, taking manufacturing operations to new heights of efficiency.
CNC has been around since the late 1950's, but continuous improvements in computer technologies and programming have made possible what seemed like science fiction just a few short years ago. The major thrust now is educating a new generation of workers to program, operate, and maximize the capabilities of these amazing robots.
Josh Schohn is the Sales Manager for Torchmate, a division of Lincoln Electric Cutting Systems. Among other things he is in charge of the company's educational outreach program. Josh bases his training philosophy on what he calls the "design/cut/weld" process. This teaches students how to bring an idea to a finished product through the process, by controlling rather than physically making the product. "I also add 'imagine' to the beginning of that process," says Josh, "and 'market', 'sell', to the back end." His goal is to provide schools, teachers, students, and industries with the educational tools to turn out highly qualified workers who can utilize the power of computer-controlled robots.
So, what can robots do in an industrial setting? Just about anything, according to Schohn. They pick materials, pull them at the proper intervals, sort, cut, weld, assemble, even pack and ship. But they don't do it all on their own - their tasks have to be envisioned and designed by humans. That's where Torchmate's educational programs come in.
Torchmate has adopted the model that Apple Computer used so successfully when they provided computers to elementary schools in the 1980s. Torchmate puts their machines into high schools and community colleges that have industrial or machine shop programs, and into technical institutes that have a similar focus. Torchmate machines are very affordable by industry standards, from around $3000 for a small 2-axis machine to around $20,000 for a larger multi-axis unit. Torchmate provides free unlimited technical support for these machines, and is rolling out a program in the fall of 2013 to provide free curriculum and unlimited CAD/CAM licensing to all teachers and students using the machines. This will enable the students to use the programs on their laptops for homework projects.
Torchmate's educational programs are not exclusive to the United States. They provide the same programs to Europe and South America, where they have a large market for their machines. The company's emphasis on education has a twofold purpose: to help speed the integration of robotic automation into industry, and as a marketing tool. Students coming out of school will have a preference for using machines they're already familiar with.
Speaking with Schohn gives you some idea of his enthusiasm for CNC-controlled robots. "They are very efficient, they work around the clock, and they never call in sick or come to work hungover," he says. Fortunately for Schohn and other sales professionals, nobody has yet developed a sales robot.
About Torchmate CNC Cutting Systems
Torchmate, a Lincoln Electric company, is headquartered in Reno, Nev. and manufactures custom CNC plasma cutting tables and other automation solutions for manufacturers worldwide. For more than 30 years, whether with a plasma cutter, router, water jet, engraver, glue gun or other tools, Torchmate has provided more options, accessories and innovations than any other CNC cutting table manufacturer. For more information, call toll free at (866) 571-1066 or internationally at (775) 673-2200, or visit the company's website, http://www.torchmate.com.
Featured Product
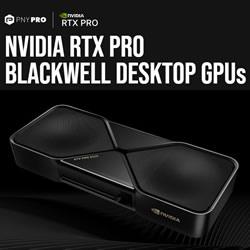
NVIDIA RTX PRO™ BLACKWELL DESKTOP GPUs
NVIDIA RTX PRO™ - Built for Professionals - NVIDIA RTX PRO Blackwell Desktop GPUs feature the latest breakthroughs in AI, ray tracing, and neural rendering technology to power the most innovative workflows in design, engineering, and beyond.