BRM Announces EASTEC 2013 Tradeshow Plans; Visit Booth # 5000 for Diamond Flex-Hone® and NamPower Surface Finishing and Deburring Tools
Brush Research Manufacturing (BRM), American manufacturer of flexible honing tools and industrial brushes, announces tradeshow plans for EASTEC 2013. California company will showcase Diamond Flex-Hone® and NamPower™ surface finishing tools in West Springfield, Massachusetts from May 14 to May 16, 2013 (Booth # 5000).
Los Angeles, CA April 30, 2013
Brush Research Manufacturing (BRM), makers of industrial brush tools and flexible hones, is announcing tradeshow plans for the Eastern States Exposition (EASTEC 2013) from May 14 to 16 in West Springfield, Massachusetts. Visit BRM at EASTEC in Booth # 5000.
Mike Miller, BRM Vice President of Global Sales, and Josh Neugass, BRM Technical Services Specialist, will represent the Los Angeles, California company and showcase its Diamond Flex-Hone® tools and NamPower™ abrasive disc brushes, complete solutions for deburring and surface finishing.
Sponsored by the Society for Manufacturing Engineers (SME), EASTEC 2013 is where forward-thinking manufacturers connect. SME is a global leader in promoting manufacturing workforce development, technological innovation, and technical information.
Diamond Flex-Hone® Tools Surface Finish and Deburr Hard Materials
BRM Diamond Flex-Hone® technology is used for deburring, edge blending, and surface finishing hard materials such as carbides, ceramics, and aerospace alloys. Precision-engineered for rapid cut rates, BRM's long-lasting diamond hones provide optimal finish and offer excellent heat dissipation.
The aerospace industry uses BRM diamond hones to surface finish aircraft structures, helicopter drive shafts, hydraulic control mechanisms, and swivel components. Military customers use BRM diamond honing tools to machine high-quality holes and avoid the loss of strength and temper.
Diamond honing tools are also ideal for surface finishing medical parts. Other manufacturers use Diamond Flex-Hone® technology to surface finish carbide wear rings, guide and drill bushings, chromed and plated bores, ceramic cylinders, and electrical discharge machining (EDM) layers.
NamPower™ Industrial Brushes Automate Deburring and Surface Finishing
BRM NamPower™ abrasive disc brushes are easily integrated into automated machinery, CNC machining centers, transfer lines, and robotic cells. Manual surface finishing and deburring tools are suitable for hobbyists, but manufacturers need NamPower™ technology for automating finishing and deburring operations with high-volume parts.
NamPower™ brush tools feature a combination of ceramic and silicon carbide filaments. These high-performance abrasive disc brushes work like flexible files, conforming to part contours while wiping and filing across part edges and surfaces. For less vibration and more repeatability, NamPower™ brushes also use a molded, fiber-reinforced thermoplastic base.
Visit BRM at EASTEC 2013 in Booth # 5000
Visit Brush Research Manufacturing (BRM) at EASTEC 2013 to see the Diamond Flex-Hone® tool and NamPower™ abrasive disc brushes. Mike Miller, BRM Vice President of Global Sales, and Josh Neugass, BRM Technical Services Specialist, will be on-hand to answer questions in Booth # 5000.
About Brush Research Manufacturing
Brush Research Manufacturing (BRM), makers of the Flex-Hone® tool, is located in Los Angeles, California. Since 1958, BRM has been solving difficult finishing problems with brushing technology. BRM's Flex-Hone® tool is the standard against which all other surface finishing tools are compared.
Featured Product
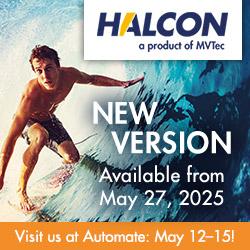
Next-Level Vision with HALCON 25.05
HALCON 25.05 sets new standards for machine vision, introducing Deep 3D Matching for robust bin picking, enhanced OCR accuracy, improved QR code reading on curved surfaces, and smarter camera integration. Meet MVTec at Automate Detroit and experience how the latest deep learning technologies and development tools empower you to create faster, more reliable, and flexible industrial solutions.