Utility Couplers and Tool Changers Safely Save Time
Tennessee Rand Utilizes ATI Products in Flexible Manuafcturing
Apex, NC, May 7, 2013
The right equipment for the right job allows Tennessee Rand Inc. out of Chattanooga, TN to manufacture Harley Davidson motorcycles parts with expert precision; safely and efficiently. Tennessee Rand offers solutions to a variety of industries from automotive, military, aerospace, and power generation to off-road/heavy equipment. They frequently use ATI Industrial Automation's Tool Changers and Utility Couplers. These components make it possible to switch between specialized tank, sub-frame, and final frame welding fixtures automatically.
Without ATI Tool Changers, manufacturers would need multiple robots to change tooling processes; now only one robot is required, saving the company time and money. Before this automatic tool change option existed, workers had to manually change tools and this caused a safety issue for workers going into work cells. Automatic tool changes eliminate human contact and are therefore much safer. Likewise, ATI Utility Couplers provide an automated method for quickly and safely connecting utilities in docking and fixturing operations.
ATI Tool Changers and Utility Couplers have proven themselves valuable at Tennessee Rand, allowing expansion not only within the company, but also within other divisions of Tennessee Rand as well. This is accomplished by creating more flexible work cells that can change-over rapidly between product variations and product lines. ATI's products allow companies like Tennessee Rand to create cutting-edge manufacturing equipment that provides customers with the most efficient robotic tooling options available. All ATI Tool Changers feature their patented Fail-Safe Locking Mechanism and No-Touch Locking™ technology. Key features include: Excellent repeatability, high rigidity, and a lightweight and compact design. ATI Utility Couplers are compatible with a large number of standard ATI Tool Changer Utility Modules.
Featured Product
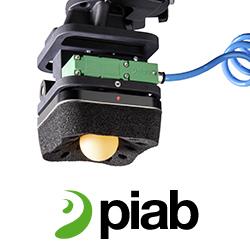
Piab's Kenos KCS Gripper
Piab's Kenos KCS gripper enables a collaborative robot to handle just about anything at any time. Combining Piab's proprietary air-driven COAX vacuum technology with an easily replaceable technical foam that molds itself around any surface or shape, the gripper can be used to safely grip, lift and handle any object. Standard interface (ISO) adapters enable the whole unit to be attached to any cobot type on the market with a body made in a lightweight 3D printed material. Approved by Universal Robots as a UR+ end effector.