Honeywell Rolls Out New Model S Series Subminiature Pressure Transducers
Designed to handle high pressure and temperatures
Featuring 1% accuracy, Honeywell Sensing and Control's Model S Series of subminiature pressure transducers fit into tight spaces with little clearance, and accurately measure pressure ranges from 100 psi to 15000 psi.
These rugged transducers are designed to handle high pressure and temperatures, with a high natural frequency and flush diaphragm for applications such as engine and transmission test stands, pressure brake testing, and hydraulic sensor testing.
Honeywell's full line of subminiature pressure transducers accurately measure pressure ranges from 100 psi to 15000 psi. These gage-only subminiature pressure transducers have a high natural frequency and utilize a flush diaphragm that is manufactured from 17-4 PH Stainless Steel. Temperature compensation is accomplished by using temperature-sensitive components located inside the transducers. These transducers have a small electrical zero balance circuit board which is in the lead wire (approximately 1 in x 0.087 in thick). This balance board does not have to be in the same temperature as the transducers. All transducers have four (4) active bonded strain gages arranged in a Wheatstone-bridge configuration.
Honeywell offers a full line of lightweight subminiature pressure transducers which feature a compact, flush mount, low profile design and flush diaphragm enabling them to fit into extremely small spaces with tight clearances. The unitized stainless steel design, with a thin diaphragm and heavy sidewalls constructed from one piece of stainless steel, makes these sensors very rugged, yet thin enough to measure low pressures. Honeywell's wet/wet subminiature differential pressure sensors offer a high degree of accuracy and pressure measurement ranges from 5 psid to 2000 psid. Their small size, bidirectional overload protection, wide temperature compensation and high natural frequencies make them uniquely suited to aerospace, chemical or nuclear applications.
Specifications:
Range - 100 psig to 15000 psig
Accuracy - 1.0 % FS BFSL
Media - Gases, liquids compatible with wetted parts
OutPut - 2 mV/V
Temperature, Operating - -54 °C to 149 °C [-65 °F to 300 °F]
Temperature, Compensated - 16 °C to 71 °C [60 °F to 160 °F]
Temperature Effect, Zero - 0.01 % FS/°F
Temperature Effect, Span - 0.02 % reading/°F
Electrical Termination - Four twisted leads (1.83 m [5 ft]) with external balance board
Mating Connector - None
Overload, Safe - 50 % over capacity
Overload, Burst - 400 % full scale
Wetted Parts Material - 17-4 PH Stainless Steel
Case Material - Stainless Steel
Honeywell offers a broad portfolio of sensors which meet industry standard approvals such as ATEX, CSA, and more, and are built tough to provide enhanced reliability, accuracy, and versatility in a wide range of test and measurement applications. Honeywell's test and measurement sensor solutions help customers worldwide in research and development, design, quality testing, manufacturing and system monitoring in many different industries, challenging applications, and rugged environments. Customized solutions are also available, so stop by the Honeywell booth for more information and to discuss your application.
Featured Product
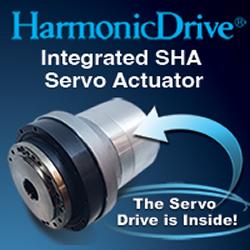
Harmonic Drive - Coming Soon! Integrated Actuators with EtherCAT®!
The IDT Series is a family of compact actuators with an integrated servo drive with
CANopen® and, coming soon, EtherCAT® . With high torque, exceptional
accuracy and repeatability, these actuators eliminate the need for an external drive and
greatly simplify cabling.