Object Scanning Autonomous Robot Wins IED Prize
Five graduates from the University of Bristol's engineering design degree have been awarded a group prize from the Institute of Engineering Designers (IED) for an automated system that could enable people to view online large exhibits held in permanent storage.
Ralph Collings, Steve Ellis, Peter Fletcher, Sophie Sladen and Eloise Taysom, who graduated this summer, have been awarded the prize for the quality of work produced within their project, entitled 'Object Scanning Autonomous Robot' (OScAR).
The Science Museum at Wroughton is home to the Science Museum's big-object store, a former Second World War airfield. As these large exhibits are not open to the public the students' brief was to develop an automated system to view objects of interest online.
OScAR consists of a floor-mounted robot supporting a flexible arm with camera and a web-based interface to view exhibits. The system was developed after investigating existing products and identifying that all had significant limitations for the proposed brief.
Based on research into museum learning and online behaviour, the online audience was segmented into five groups: general public, website visitors, casual browsers, learners and experts. For each group, recommended user interface features were identified to ensure the system addresses the user needs. A model was developed to show how the percentage of users in each segment could be monitored by tracking website interaction to understand how the website is used, so that the site could be continually improved.
Sophie Sladen, one of the winners, said: "It was great to be involved in an industry sponsored, interdisciplinary project at the cutting edge of technology. It is exciting to think that the end result can be put into practice both for the Science Museum and potentially for a wide range of other uses including disaster relief."
Dr Paul Harper, Lecturer in Engineering Design and Engineering Design Year 4/5 Projects Co-ordinator, added: "This is a shining example of the success achieved by our students when working in partnership with industry on applied research and design projects during the final two years of their degree."
Investigation into the market for the proposed system revealed that 22 per cent of UK museums were forced to close exhibit spaces in 2011-12 as a result of austerity measures. By employing the OScAR system, museums could reduce their overheads whilst maintaining public access to their collections.
The OScAR system could also be adapted for other applications and markets such as capture of 3D data for film and video game production, a remote observation vehicle for disaster zones, inspection of large engineering structures, augmented reality and haptic interfaces.
To bring the system to market, the further development cost would be £70,000, with an estimated payback time of 12 months. Future work on the system should focus on the full integration of a complete arm and robot control system, implementation of a navigation control algorithm and more detailed specification of chassis components.
The OScAR project, in collaboration with NSN and the Science Museum, was supervised by Dr Steve Burrow and Mervyn White from the Department of Aerospace Engineering.
Mervyn White, Teaching Associate in the Department of Aerospace Engineering, said: "The team did a great job in challenging the expectation for this project with an alternative and very novel approach. They developed existing research and blended it with innovative design and problem solving to deliver an outstanding result that has been recognised with this IED award."
A video demonstrating the OScAR system and its robotic arm is available on http://www.youtube.com/watch?feature=player_detailpage&v=7OV_ywXx8k8.
A video demonstrating the OScAR system and its movement and scene reconstruction is available on http://www.youtube.com/watch?feature=player_detailpage&v=PJPcmtZF1Y0.
Featured Product
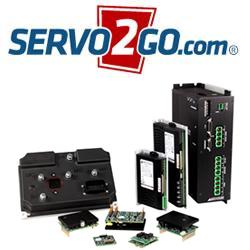
High Performance Servo Drives for localized and distributed control applications from Servo2Go.com
Engineered to drive brushless and brush servomotors in torque, velocity or position mode, Servo2Go.com offers a broad selection of servo drives in a wide range of input voltages and output power levels.