FANUC's Industrial Robots and Automation Help EMP Compete Globally
FANUC America Corporation has released a new YouTube video highlighting Engineered Machined Products (EMP), an Escanaba, Michigan-based manufacturer competing globally with the help of robotic automation.
The video showcases EMP's commitment to market and product diversification as an increasing number of its customers are "on-shoring". Automation systems in place at EMP have been instrumental in allowing the company to meet increasing demands. With industrial robots and automation, EMP is able to compete globally, expand its business, and remain a strong and viable manufacturer based in Michigan.
"Our investment in automation has enabled us to compete effectively across the globe," said Jerry Guindon, vice president of sales for EMP. "Our owner Brian Larche is dedicated to our community, so the implementation of automation really made a big difference and allowed EMP to keep the jobs here in Michigan -- automation saved jobs."
About EMP
EMP is ISO/TS certified and along with being a world-class manufacturer of machined pumps and complex components for use in the heavy-duty diesel engine and hydraulics markets, EMP is also a leader in the design, manufacturing and assembly of advanced thermal and oil management components and systems. EMP's advanced innovative technologies are designed to significantly improve engine cooling, increase fuel economy, reduce emissions and increase overall operating efficiencies. EMP offers state-of-the-art R&D capabilities and competes globally on precision machining, utilizing the latest in automation and advanced robotics.
Source: http://www.fanucamerica.com/
Featured Product
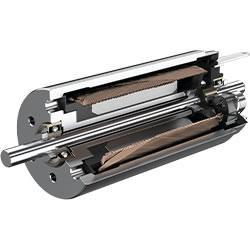