Mind-Reading Robots Coming Ever Closer
The University of Cincinnati's College of Engineering and Applied Science (CEAS) will host the symposium on Nov. 14-17 at UC's Kingsgate Marriott Conference Center.
Nov. 14, 2013 - If you think with the release of every new i-device the world is getting closer to thought-controlled smart tech and robotic personal assistants, you might be right.
And thanks in part to work led by the University of Cincinnati's Anca Ralescu, we may be even closer than you realize.
Professor Ralescu of the Department of Electrical Engineering and Computing Systems will discuss her team's research aims and current progress on brain-computer interface at the International Human-Centered Robotics Symposium (HuCeRo). The University of Cincinnati's College of Engineering and Applied Science (CEAS) will host the symposium on Nov. 14-17 at UC's Kingsgate Marriott Conference Center. The symposium aims to bring together leading researchers and engineers in the fields of robotics, computer science, material science and brain-computer interaction. Ralescu's presentation will be Nov. 17.
Brain-computer interface uses electroencephalography (a measure of the brain's electrical activity) to help distinguish which brain signal corresponds with the body's performance of a particular intended action. In these experiments, Shikha Chaganti, a graduate student in computer science advised by Ralescu, specifically targeted brain impulses generated when a person thought about going from a sitting position to standing and vice versa. Computers process this data -- which can be reinforced by combining it with measures of electrical activity in muscle -- in order to detect these brain signals and interpret their intent. The idea is to allow a person to use thought alone to communicate with a computer about the intent to move.
"The problem is quite difficult," Ralescu says. "We are experimenting with processing the signal and selecting useful features from it, and designing a classifier capable of distinguishing between the these two transitions -- sitting to standing and standing to sitting."
Ralescu's work eventually could be used in conjunction with another project being presented at HuCeRo by UC's Gaurav Mukherjee, a master's student in mechanical engineering in UC's College of Engineering and Applied Science (CEAS), and Grant Schaffner, an assistant professor in UC's Department of Aerospace Engineering and Engineering Mechanics. Mukherjee and Schaffner designed and built a spring-assisted leg exoskeleton that can help people with impaired mobility. By integrating Ralescu's brain-computer interface into the exoskeleton, someone using the device could think, "I'm going to stand," and they'd receive a robotic boost as they rose to their feet.
Ralescu also says HuCeRo will feature discussion of UC's development of an interdisciplinary curriculum for human-centered robotics.
"The idea of human-centered systems in general, and human-centered robotics in particular, is not new. But to some extent things were just not in place. Some technology or other was either missing or too expensive," Ralescu says. "To my knowledge, there is no formal curriculum in this area in any university. If UC moves forward with creating such a curriculum, it could be among the first of its kind. So UC would be a pioneer in establishing such a curriculum."
In addition to the contributions from UC graduate students Chaganti and Mukherjee, Ralescu's work has benefited from interaction with Jonathan Adam Wilson, a postdoctoral fellow in pediatrics at UC and of Cincinnati Children's Hospital Medical Center; Tomasz Rutkowski of the University of Tsukuba and the Brain Science Institute at RIKEN in Japan; and Christoph Guger, CEO of Guger Technologies in Graz, Austria.
Featured Product
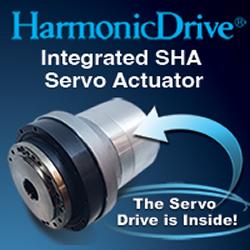
Harmonic Drive - Coming Soon! Integrated Actuators with EtherCAT®!
The IDT Series is a family of compact actuators with an integrated servo drive with
CANopen® and, coming soon, EtherCAT® . With high torque, exceptional
accuracy and repeatability, these actuators eliminate the need for an external drive and
greatly simplify cabling.