Stronger focus on optimised material usage
LASYS 2014: Laser production systems for material processing are becoming more and more precise and efficient
New aspects are becoming apparent! With laser production system manufacturers experiencing pressure for decades to offer improved performance at more reasonable prices, according to Volker Krause, Managing Director of Laserline GmbH, another trend is now catching on: "Users are looking much more precisely at the solution of their application. Laser production systems are becoming more and more diversified and, besides the costs, greater attention is now also being paid to performance, quality and flexibility."
At the next LASYS 2014, the international trade fair for laser material processing, which opens its doors at the Stuttgart trade fair grounds from 24 to 26 June 2014, this paradigm shift will also be noticeable. Last year LASYS registered a huge increase in the number of visitors. This reinforces once again the concept of both a cross-industry and cross-material trade fair, which is aimed explicitly at material processing using laser.
Improved production process efficiency with laser production systems
The laser industry is increasingly gaining ground on account of the enormous variety in applications and materials covered by laser production systems. For instance, the global market for laser production systems grew by nine percent to 7.9 billion Euro in 2012 compared to the previous year. The majority of the roughly 75% represented laser systems for macro-processing and the remaining quarter could be attributed to micro-applications which are becoming more and more interesting. The market data is based on information provided by the VDMA working group "Laser and Laser Systems for Material Processing", a professional and conceptual supporter of LASYS, taking into consideration the evaluations of Optech Consulting. Equally responsible for the market growth is the fact that production system manufacturers and operators are being increasingly won over: Laser systems contribute greatly to increasing the efficiency and productivity of a machine or system. "Above all, when the focus is on the production process as a whole", states Gerhard Hein, Managing Director of the working group "Laser and Laser Systems" in the VDMA, "energy efficiency first becomes visible." The reasons are obvious: sustainable and optimised material usage due to laser material processing, increased processing quality with fewer post-treatment steps, high production speeds, high flexibility and minimal changeover times. "This leads to competitive advantages thanks to high process efficiency and reasonable overall costs per component", continues Hein.
Sophisticated technologies with diode lasers
Increasingly sophisticated technologies are doing their utmost to improve efficiency. An example is the diode laser, which recently is now being used for more and more applications. The direct conversion of electrical to optical energy permits a particularly high degree of overall efficiency. As a result of the boost in power densities in recent years for diode lasers, they are also now used for deep penetration welding applications, as well as welding galvanised sheets and aluminium, for example in the automotive industry. Owing to the good absorption properties for diode laser light, the welding is particularly stable, efficient and does not require any reworking. Laserline will further expand its diode laser development activity to special fields of work up to the next LASYS 2014. "These fields will be in the area of small focus diameters and so-called remote applications", states Krause.
Laser coatings replace hardening processes
Diode lasers with higher power can, for example, obtain high soldering speeds, as is required in the roof seam in vehicle production. They also deliver high coating rates for the application of wear protection layers. Laser deposit welding is also an excellent example where laser production systems are increasingly replacing conventional methods. "The laser coating is increasingly replacing traditional hardening processes in the area of industrial steel processing, for example with the coating of rollers", states Dr. Daniel Wildmann, Managing Director of Sales and Marketing at Precitec KG. Other applications include the coating of drill heads and hydraulic cylinders. Laser coating is a process which increases the wear, corrosion and impact resistance of metal components. A weld pool is created using a high-power, precision-focussed laser beam, which is fed to the metal powder. "Due to the precision of the laser beam a completely thick coat with minimal dilution and a perfect metal composite can be achieved", adds Dr. Wildmann. The Precitec team presents its systems and know-how at LASYS 2014.
Ultrashort pulse laser systems ready to be put into practice
Ultrashort pulse lasers have been all the rage in recent years. They are shifting more and more from the laboratories to industrial production. This includes lasers which are pulsed in the picosecond or femtosecond range. Their application is designed for micro-processing - for example in the production of semiconductors, high-resolution displays, solar panels, instruments for medical technology, as well as in the aerospace industry. "This laser class only realises its full potential when the complete system is suitable for industrial use and is user-friendly", highlights Eduard Fassbind, Managing Director of Swisstec Micromachining AG. This is why the fast and very precise femtosecond laser production systems from the Swiss engineering company are also based on a modular principle and can be tailored precisely to the user. They were developed taking into account efficiency and "Green Energy". "Compact cooling units, based on Peltier elements, only require a fraction of the original space and also consume less energy", explains Fassbind. LASYS 2014 will showcase the latest compact systems.
High-quality printed circuit board boreholes at high throughput rates
The most important requirement of laser and laser production systems in the manufacture of semiconductors is the suitability for industrial applications, because the tough manufacturing conditions in a triple-shift operation, for example in the manufacture of printed circuit boards, must be overcome. "Users from the semiconductor industry demand high reliability in laser power control, as well as pulse-to-pulse stability", states Klaus Löffler, Manager of International Sales and Marketing at Trumpf Laser- und Systemtechnik GmbH. A typical example is modern printed circuit boards, which nowadays are multilayered. The wiring is effected via boreholes with diameters less than 100 µm, which are then filled with copper. "At Trumpf we have developed a controller which monitors each individual laser pulse and maintains the power and pulse energy at the required level regardless of external influences. It is thus possible to realise reproducible results on the workpiece - even with the complex material mix of copper, glass fibre and resin", states Löffler. The high pulse peak energies for ultrashort pulse lasers permit the processing of these composite systems in a single work process. The desired geometry and quality are reliably achieved, and at throughput rates of well over 1,000 holes per second.
LASYS 2014 promises to be exciting - a comprehensive first-class framework programme will also add to the event: The short course "Basic knowledge of lasers and laser material processing" for visitors, who have little or no experience with lasers. The forum "Lasers in Action", at which exhibitors show how innovative laser systems are used in practice using current case studies. The Solution Center "Meet the experts", at which independent experts from well-known German laser research institutes are on hand to answer questions from visitors on laser production. The "Stuttgart Laser Technology Forum (SLT)" with contributions from well-known representatives from industry and science on current trends in laser technology and best-practice examples. And the "Stuttgart Laser Marketplace", a seminar about markets and trends in the area of laser material processing.
In addition, the UKIP automotive trade fairs, as well as O&S, international trade fair for surface treatments and coatings, are taking place parallel to LASYS, and also for the first time parts2clean for industrial parts and surface cleaning, which is an excellent and relevant addition and gives the trade fair visitor synergy effects.
Featured Product
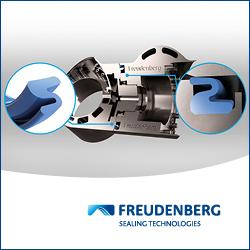