Yaskawa Motoman MA1440 Welding Robot Offers Improved Welding Speed
More energy efficient and designed for improved maintainability
Dayton, OH - Sleek, strong and fast, the new 6-axis MA1440 arc welding robot features a 6 kg payload, up from 3 kg on the MA1400 model. Additionally, compared to the MA1400, the new MA1440 features a 23% larger wrist hole for utilities and is up to 15% faster. The MA1440 robot is introduced with the new DX200 robot controller which is more energy efficient and designed for improved maintainability.
The MA1440 features a new contoured arm structure that reduces interference by enlarging the close-range motion area of the robot, making it optimal for welding large workpieces and reaching over jigs. The upper arm shape also provides an improved mounting area that allows more room for the feeder. Available in floor-, wall- or ceiling-mounted configurations and ideal for high-density layouts, the space-saving MA1440 robot increases productivity due to its Sigma-5 motor control technology.
The MA1440 robot has a 1,440 mm (56.7") horizontal reach, 2,511 mm (98.9") vertical reach and ±0.08 mm (±0.003") repeatability. Its integrated through-the-arm torch cabling eliminates cable interference, simplifies programming and reduces cable wear. The enlarged 50 mm thru-hole can allow signal cables for sensors, higher current cables and water-cooling lines. The higher payload allows motorized torches and cameras to be mounted on the wrist for welding applications. Additionally, a material handling version of the robot with a 12 kg payload is available (MH12).
The MA1440 robot uses the new Yaskawa Motoman DX200 controller that features patented multiple robot control technology to easily handle multiple tasks and control up to eight robots (72 axes), I/O devices and communication protocols. Its extensive I/O suite includes integral PLC and HMI pendant displays, high-speed Ethernet communication, 4,096 I/O addresses and a graphical ladder editor that can provide system level control. The DX200 has been designed to improve process capability, reduce energy usage, and improve maintainability and safety. An enhanced Functional Safety Unit (FSU) provides control reliable zone and tool position monitoring, stand still monitoring and speed limiting. This can reduce costs for safeguarding hardware and provides new capabilities such as collaborative tasks. It is compliant to ANSI/RIA R15.06-2012 and other relevant ISO and CSA safety standards.
About Yaskawa Motoman
Founded in 1989, the Motoman Robotics Division of Yaskawa America, Inc. is a leading robotics company in the Americas. With over 270,000 Motoman® robots installed globally, Yaskawa provides automation products and solutions for virtually every industry and robotic application; including arc welding, assembly, coating, dispensing, material handling, material cutting, material removal, packaging, palletizing and spot welding. For more information please visit our website at www.motoman.com or call 937.847.6200.
Featured Product
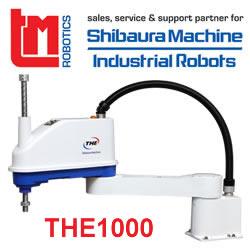
TM Robotics - Shibaura Machine THE SCARA range
The THE range from Shibaura Machine is an extensive line up of SCARA robots. Available in four arm lengths THE400 (400mm), THE600 (600mm) and the most recent THE800 (800mm) and THE1000 (1000mm), this range is suitable for assembly, handling, inspection and pick and place processes in varied industrial applications. The THE1000 boasts a 20kg payload capacity and an impressive 0.44 second cycle time, providing high speeds for processes with large components. In fact, the range has been recognised for as the price-to-performance leader compared to other SCARA models in its price range due to its impressive speed versus payload capacity.