Gripping Systems
Profinet module with integrated safety technology
The heavy-duty handling systems of the family-owned company are available in sizes 210, 310, 510, and 1210. They are specifically designed for the handling of heavy workpieces and tools. At its four outer surfaces different pneumatic, fluidic, and hydraulic modules, servo and bus modules, welding current modules, coax and fiber optic modules of the robot accessories program from SCHUNK can be attached. The quick-change heads and adapters are pneumatically coupled with each other via a patented self-retaining locking system. Thereby a "no-touch locking system" ensures that the module can be already locked at a distance of 2.5 mm.
Featured Product
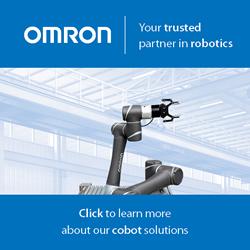
Discover how human-robot collaboration can take flexibility to new heights!
Humans and robots can now share tasks - and this new partnership is on the verge of revolutionizing the production line. Today's drivers like data-driven services, decreasing product lifetimes and the need for product differentiation are putting flexibility paramount, and no technology is better suited to meet these needs than the Omron TM Series Collaborative Robot. With force feedback, collision detection technology and an intuitive, hand-guided teaching mechanism, the TM Series cobot is designed to work in immediate proximity to a human worker and is easier than ever to train on new tasks.