Converting Diverter Dampers from Stone Wool to Superwool® Blanket Yields Labor and Fixture Savings
When Esscano Power A/S wanted to improve its diverter damper insulation from mineral wool (rock wool) material, the company examined all the available alternatives, ultimately locating numerous online references to high temperature insulation wool from Morgan Advanced Materials.
When Esscano Power A/S wanted to improve its diverter damper insulation from mineral wool (rock wool) material, the company examined all the available alternatives, ultimately locating numerous online references to high temperature insulation wool from Morgan Advanced Materials. After heat calculations demonstrating that its Superwool® Plus blanket material would reduce total insulation thickness were provided, Esscano was ready to make the switch. The change has been extremely successful, reducing labor costs due to the speed of installation compared to mineral wool, along with yielding a number of additional savings from items such as fixings and associated metalwork.
Denmark-based Esscano Power is a leading manufacturer and supplier to the industrial damper market worldwide. Looking for alternatives to its current mineral wool insulation, the company had been pursuing a variety of other refractory ceramic fibre (RCF) options when they contacted Morgan for information regarding their range of Superwool® low bio-persistent insulating fibre products, an alternative to traditional refractory ceramic fibre insulation. The Superwool® range is exonerated from Carcinogen classification in Europe under Nota Q of Decision (EC) N°1272/2008.
After receipt of the enquiry, Elaine Hughes, regional business development officer for Morgan Advanced Materials, was convinced Esscano would be best served by switching over to Superwool Plus. She provided Esscano with the relevant products specific features and benefits to explain why it was a superior product, and recommended Superwool Plus Blanket in a 50mm thickness and 128kg density.
"Our Superwool Plus blanket ticked all the important technical boxes for the project," said Elaine Hughes, including thermal conductivity, shrinkage and temperature capability and it also offered an improved fixing pattern. Morgan provided all relevant technical details, including the published data giving clear evidence of its ability to meet the customer's performance needs. They also supplied examples of previous success stories.
Morgan followed up with several meetings with the Esscano team in Denmark to reassure those who had reservations and questions about the product. They emphasized product availability, exceptional customer support, including specialist knowledge with export documentation, and improved product packaging. They also demonstrated reduced installation costs and showed how the product would be easier to handle and give a much more eye-pleasing result when installed.
Superwool Plus low bio-persistent insulating fibre products are 17 percent more energy efficient than traditional RCF and any other alkaline earth silicate (AES) insulations. It is ideal for furnace linings in the iron and steel and aluminum industries, as well as other applications requiring high temperature processing. This enables users to increase manufacturing process efficiencies and make significant cost savings associated with energy usage.
The material provides excellent insulation in high temperature environments with a classification temperature of 1200°C (2192°F). A breakthrough in the company's advanced manufacturing control has allowed the product to be engineered to maximize the fibre content. As a result, it has up to 20 percent lower thermal conductivity than competitive insulations - and enhanced energy saving properties with much improved handleability.
Superwool Plus delivers high performance with a higher fibre index and blanket thickness than alternative products, enabling customers to use less insulation and make weight and cost savings. For example, a thinner insulation blanket, such as the Superwool Plus (96kg/m3)(6 pcf) can be used to provide the same insulation as a typical (128kg/m3)(8 pcf blanket).
Figure 1 shows the installation of the Superwool Plus blanket. Esscano used a fabrication facility close to the end user site.
The Superwool Plus blanket has high tensile strength and good handling ability. In addition to the blanket form, used in the Esscano application, Superwool Plus also comes as blanket modules, Pyro-Bloc® modules, paper and lubricated bulk making it easier for handling (available as chopped and unchopped). Felt, vacuum formed products and board varieties are also available.
The Esscano installation was cost neutral because mineral wool's lower material costs are largely offset by higher installation costs compared to those of Superwool Plus blanket. Along with lower installation costs due to the speed of installation, the blanket has improved handling, which also results in lower waste costs. Since it has a much higher temperature performance, Superwool Plus blanket offers greater security in case of any major temperature over run.
After being introduced to Superwool Plus, Esscano is confident in saying that it is the product of choice for this application. Also, the success of the Esscano project in the Middle East using products from Morgan Advanced Materials has opened up more opportunities for the young and dynamic company, and has been included in more tender documents.
Featured Product
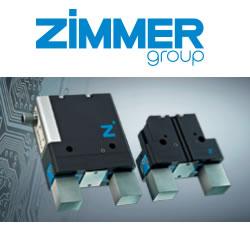