Introducing Glide-Line Multi-Strand Pallet Handling Conveyor System.
Glide-Line ™ offers the most versatile multi-strand panel and pallet-handling conveyor solution available for PV panel handling technology that takes in consideration the demands of the solar industry.
Souderton, PA, April 3, 2014 - Glide-Line ™ offers the most versatile multi-strand panel and pallet-handling conveyor solution available for PV panel handling technology that takes in consideration the demands of the solar industry. Wafer-based solar module manufacturing processes are extremely sensitive, demanding smooth vibration-free, clean and efficient transport.
Glide-Line's proven transfer technology is ideal for high volume production projects and top quality performance. Glide-Line's understands the concern of sensitivity for transporting the modules. "Stress can cause almost invisible microcracks in photovoltaic modules which once installed lead to a loss of power," says Kevin Mauger, Glide-Line's President. "Glide-Line tests every system to ensure low friction and in the evaluation process holds to a high standard ensuring compatibility for ISO and ESD environments." The Multi-Strand Pallet Handling Conveyor System is the foundation of the Glide-Line System. The Conveyor is designed to transport PV panels through the assembly process. Transport conveyors offer multiple connection alternatives to suit a variety of assembly system requirements and are available with multiple power input options as well, including 24 VDC motors. Sizes of the systems range from a minimum width of 140mm to as many tracks as required.
Benefits include
• Optional patent pending centerline adjustable conveyor
• Configurable models for SolidWorks use
• All Glide-Line systems utilize T5 timing belts with steel tension members for positive drive, durability and reduced maintenance
• All maintenance operations including belt changes can be performed from the top eliminating the need to disassemble or remove ancillary equipment.
• Drive shaft 14mm, End roller 28mm, Drive pulley 5mm pitch, 40 tooth
• B14 flange motor - 218ft / minute
• 24VDC direct drive option for ultra-quiet maintenance free operation, absence of gearbox and connecting shafts offer ultimate design flexibility
• All rolling elements are precision ball bearing supported for long ultra-quiet, high-load maintenance free operation
• Multiple, mounting drive configurations available AC single, 3 phase options, as well as 24VDC options
Information about Glide-Line - Glide-Line, a subsidiary of NCC Automated Systems has helped clients overcome automation and material handling challenges for over 25 years. Within NCC's customer portfolio are some of the longest established brands including The Hershey Company, PepsiCo, Unilever, General Mills, Starbucks, Procter & Gamble and Satisloh North America. In 2013 NCC Automated Systems and all business units developed, produced and delivered over 15 million in US dollars employing over 50 employees.
Glide-Line contact - Chris Round, Director of Marketing cround@glide-line.com 513-550-2820
Featured Product
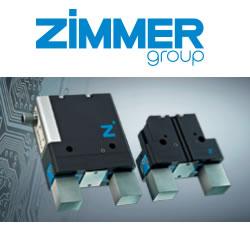