Seegrid Lean Project Manager Chiocchio Focused on Efficiency and Lean Management
Chiocchio gained most of his lean experience and training over the past 21 years, first working as a manufacturing manager at Sony Electronics.
PITTSBURGH, PA—Seegrid Corporation, the leader in robotic vision-guided automated guided vehicles (AGVs), recently continued staff expansion to meet product demand. The Pittsburgh-based robotics leader welcomed Tim Chiocchio as the new lean project manager.
Chiocchio shared his excitement about joining the Seegrid team, "The biggest factors in joining Seegrid relates directly to the culture set by the management team. The entrepreneurial spirit of its employees and the overall vision the company is addressing with automated solutions will pioneer new frontiers in material transportation for manufacturing, distribution, and warehousing. These efforts make our customers safer, productive, and ultimately more stable and competitive." Chiocchio will report to John Mazock, Vice President of Manufacturing.
Mazock noted, "In looking for a person that could support customers with lean initiatives, I needed to have someone that could ‘walk the walk. Chiocchio is exactly that person. He has the ability to go into a facility, identify opportunities for improvement, and provide support for a successful implementation."
Chiocchio gained most of his lean experience and training over the past 21 years, first working as a manufacturing manager at Sony Electronics. Chiocchio was trained under the Toyota Production System Principles and gained vast experience in lean and its application to production process improvement and material flow. Chiocchio became a Six Sigma Black Belt and ultimately was responsible for coordinating, implementing, and sustaining all continuous improvement kaizen activity. He had several opportunities to visit other Sony television and other electronic manufacturing plants in the United States, Mexico, Japan, and South Korea. Participating in these kaizen events provided valuable training in process improvement activities and capturing best practices.
About Seegrid
Seegrid Corporation (www.seegrid.com) is the global leader of robotic vision-guided automated guided vehicles (AGVs). Seegrid AGVs are revolutionizing the movement of materials handling in manufacturing and distribution environments with simplicity, flexibility, and affordability. Robotic pallet trucks, tow tractors, and walkie stackers optimize workflow processes by increasing productivity and reducing labor and operating costs, creating economic and operational advantages. Seegrid AGVs improve workplace safety, reduce equipment and product damage, and deliver a rapid return on investment. The companys state-of-the-art navigation technology requires no infrastructure for navigation—no wires, lasers, tapes, or magnets.
Guided by Seegrid partnerships with leading global industrial truck manufacturers provide businesses with a choice when selecting a brand of robotic vision-guided AGVs. Seegrid and Guided by Seegrid products are available in North America and Europe.
In addition to the 2014 Edison Award, Seegrid was named Manufacturer of the Year and the Food Logistics Top 100 software and technology providers. Follow on Twitter @Seegrid.
Featured Product
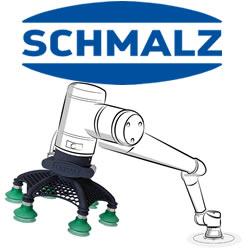
Schmalz Technology Development - The Right Gripper for Every Task
In order to interact with their environment and perform the tasks, lightweight robots, like all industrial robots, depend on tools - and in many cases these are vacuum grippers. These form the interface to the workpiece and are therefore a decisive part of the overall system. With their help, the robots can pick up, move, position, process, sort, stack and deposit a wide variety of goods and components. Vacuum gripping systems allow particularly gentle handling of workpieces, a compact and space-saving system design and gripping from above. Precisely because the object does not have to be gripped, the vacuum suction cupenables gapless positioning next to each other.