ABB introduces the FlexMT, a flexible, pre-engineered system to tend machine tools with vision guided robotics
The turnkey system increases machine tool utilization by up to 60%, can handle most any part, and is compatible with a wide range of machine tools • Increased productivity: Increased spindle utilization by as much as 60% • Reduction in operational costs: Suited for small batch runs and volume production • Standardized, flexible and simple: Pre-built, quick installation, easy programming • Health & Safety: Improved working environment
AUBURN HILLS, Mich. (August 6, 2014) - ABB Robotics has introduced the FlexMT™, a flexible, pre-engineered system designed to load and unload machine tools using vision guided robotics. Designed for both small batch and high volume production, the FlexMT increases spindle utilization by up to 60% over manual machine tending. The system can handle most any size and type of part, and is compatible with a wide range of machine tools, including horizontal and vertical lathes, machining centers, 5-axis machines and grinders.
Available in two variants: the FlexMT 20, which features an ABB IRB 2600 robot, with a 20kg payload and a 1.65m reach; and the FlexMT 60, which features an ABB IRB 4600 robot, with a 60kg payload and a 2.05m reach. The turnkey automation system comes complete with a robot controller inside its fully integrated control cabinet, providing easy and precise control of the robot, vision, conveyors and machine tool.
"ABB puts a lot of effort into creating solutions which are truly innovative and address the real needs of our customers," says Frank-Peter Kirgis, global business line manager for ABB. "With the FlexMT weve hit many of our customers leading concerns. The solution is easy, fast and flexible to set up and program; all things our customers demand. The FlexMT can also give small and medium size companies a higher degree of automation."
By facilitating a steady and predictable machine tool utilization of up to 90%, the FlexMT increases the approximate 50% spindle utilization of manual machine tending by as much as 60%. This provides a sustainable competitive advantage and a ROI in many cases of less than a year.
Additional system benefits include:
• Reduced operational cost and complexity: The vision guidance component reduces operational cost and complexity by allowing the FlexMT to recognize variations in part size and geometrical shape, and enabling it to pick and place parts that are presented on the conveyor in differing positions. The FlexMT can be used with existing machine tools and can run free from operator supervision for up to eight hours.
• Easy system set-up and programming: Control and communications with the robot are tightly integrated into the software, providing a very simple and intuitive set-up and teach-in. With one of the easiest to use operator interfaces on the market, teaching of a new part is possible in less than 10 minutes.
• Improved health and safety: The self-contained nature of the FlexMT improves working conditions by drastically reducing workplace injury related to heavy lifting, exposure to hazardous conditions including the presence of coolants, sharp edges, burrs, tooling and other dangers.
About ABB
ABB (www.abb.com) is a leader in power and automation technologies that enable utility and industry customers to improve their performance while lowering environmental impact. The ABB Group of companies operates in around 100 countries and employs about 150,000 people.
About ABB Robotics
ABB Robotics (www.abb.com/robotics) is a leading supplier of industrial robots - also providing
robot software, peripheral equipment, modular manufacturing cells and service for tasks such as welding, handling, assembly, painting and finishing, picking, packing, palletizing and machine tending. Key markets include automotive, plastics, metal fabrication, foundry, electronics, machine tools, pharmaceutical and food and beverage industries. A strong solutions focus helps manufacturers improve productivity, product quality and worker safety. ABB has installed more than 200,000 robots worldwide.
Featured Product
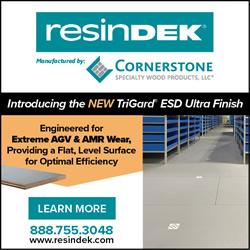