IMTS 2014 - BRM Flex-Hone® Tools at IMTS 2014 (Booth N-7163): Brush Research Announces International Manufacturing Technology Show (IMTS) Plans; Publishes Technical Resources
Brush Research Manufacturing (BRM), global supplier of flexible hones and industrial brushes, announces plans to attend the International Manufacturing Technology Show (IMTS) from September 8 to 13, 2014 in Chicago, Illinois. At IMTS 2014, visit BRM in Booth N-7163 to learn more about surface finishing and deburring solutions such as Flex-Hone® tools for inner diameter (ID) applications.
Los Angeles, CA August 27, 2014
Brush Research Manufacturing (BRM), American-owned supplier of flexible honing tools and a full line of industrial brushes, is announcing plans to attend the 2014 International Manufacturing Technology Show (IMTS) from September 8 to 13 at Chicagos McCormick Place. The brush manufacturer is also announcing the release of a new technical article and IMTS video about BRM Flex-Hone® tools.
IMTS 2014 is one of the worlds largest industrial tradeshows. With over 1 million sq. ft. of exhibit space and more than 1900 exhibitors, this years event will showcase over 15,000 products, technologies, and processes. Held just once every two years, IMTS spans nine pavilions and includes conference sessions where members of the manufacturing and machine tool industries can learn from thought leaders.
Automated Deburring and Surface Finishing
As BRMs new technical article explains, the Flex-Hone® tool is the industry standard for inner diameter (ID) burr removal and surface improvement. Flexible hones mount in most rotating spindles, including CNC equipment, drill presses, lathes, milling machines, and robotic arms. Built with a double-wire stem, these cylinder hones secure easily in chucks, collets, and similar holding devices.
With CNC equipment and machining centers, a CAT 40 collet or Jacobs-style cuck is recommended. Some manufacturers use flexible cylinder hones with handheld power tools, but automated surface finishing and deburring supports greater part consistency. Flex-Hone® tools are available for any type or size cylinder, and help manufacturers make the most of production equipment.
Burr Removal, Surface Finish Improvement, and Ease-of-Use
As BRMs new Flex-Hone® video shows, flexible honing imparts a uniform series of oil-retaining grooves for optimum lubrication. Plateau finishing leaves the base metal undisturbed, but removes raised areas (burrs) that can affect dimensional tolerances and cause part misalignments. BRMs flexible cylinder hones are also used for edge blending and cross-hole deburring.
Flex-Hone® tools or ball hones feature abrasive globules that are permanently laminated to flexible nylon filaments. These cylinder honing tools come in 10 different abrasive types and 11 grits, and are available for bores ranging in size from 4 mm to 36". For harder materials such as ceramic, carbide, and aerospace alloys, use the BRM Diamond Flex-Hone®.
Visit BRM at IMTS 2014 (Booth N-7163).
From September 8 to 13, 2014 BRMs technical specialists will be at IMTS 2014 to answer questions about Flex-Hone® tools, NamPower nylon abrasive brushes, and the California companys full line of industrial brush tools. As BRMs new technical article explains, visitors to Booth N-7163 and invited to bring in their most challenging part, and learn more about surface finishing and deburring solutions.
About Brush Research Manufacturing
Brush Research Manufacturing (BRM), makers of flexible honing tools and a full line of industrial brushes, is located in Los Angeles, California. For over 55 years, BRM has been solving surface finishing challenges with brushing technology. BRMs Flex-Hone® tool is the industry standard against which all other ID surface finishing solutions are compared.
Featured Product
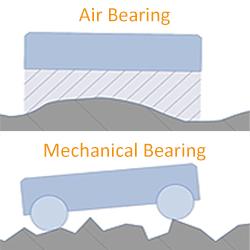
PI USA - Hexapods for 6-Axis Precision Automation
PI Hexapods simplify multi-axis alignment / positioning with a programmable pivot point, tool/work coordinate systems, virtual programming software.