VALERI Project Aims to Make Robots that Work Alongside Humans
Trying to squeeze into small enclosed areas, carrying out highly repetitive tasks, retiring with back injuries even while your expertise is needed: these everyday realities of working in aviation construction may become a thing of the past.
By helping to bring robots onto the factory floor to carry out the uncomfortable and tedious tasks, the VALERI project hopes to place a higher value on human know-how.
Car manufacturers have been using stationary robots to help build their products for years, but airplanes are constructed differently, posing challenges to the use of robotics. Until now, the manner in which planes are built and put together has meant that shifts of workers carry out assembly and inspection. ‘If we can solve the very complicated technical hurdles that prevent widespread uptake of robots in production, we can free-up people to work on the more value-added work, explains the VALERI Projects Coordinator, Mr Jose Saenz.
The industry is booming and such research will consolidate its already considerable growth. AreoSpace and Defense Industries figures show that in 2012, just under 500 000 people worked in the aerospace sector, which generated a revenue of EUR 128 billion, up from 458 000 people and EUR 107 billion in 2010.
Valeri (Validation of Advanced, Collaborative Robotics for Industrial Applications) is supported by the European Commission under the 7th Framework Programme (‘Factories of the Future Public-Private Partnership). It brings together seven partners from Spain, Germany and Austria who are building a working laboratory prototype and and will verify it in a factory setting. By 2015 the consortium plans to develop applications and test mobile robots that could later be integrated in the production of aerospace components.
These ‘mobile manipulators will be able to access small spaces and, although challenging to the programmers, the goal is to have them working on similar tasks, in multiple locations. A key hurdle to overcome is the complex programming demanded by the fact that the robots will not be static or performing identical tasks in repetitive sequence.
Producing quality work, safely
The projects scope is ambitious: not only will the robots have to work with high precision but they will need to do so while moving around humans. Currently in the manufacturing sector, robots have been segregated from the people working on the shop floor, ‘We have to make sure we have the necessary technology in place to make collaboration possible, says Mr Saenz. Tactile sensors and computer vision will permit sophisticated programming designed to stop a robot in its tracks should there be any chance of danger.
The emphasis is clearly on safety, both for the sake of the people working alongside the robots but also regarding the industrys low tolerance for error. ‘The results need to be as good, or better, than those achieved by humans, Mr Saenz explains. To make sure the machines can carry out their processes with the required quality; robots will pass over what they have done with a camera to inspect their results, verifying that everything has been carried out to the necessary standard.
The potential benefits are clear. Repetitive strain injuries and back problems necessitating sick leave, or even retirement, can be avoided. An ageing workforce with valuable expertise can be preserved as physically demanding tasks are farmed out to machines. The cost of production can be kept competitive, ensuring manufacturing isnt outsourced to cheaper markets, ‘Designers and engineers benefit from having production near at hand to get the feedback they need and inspire innovation, Mr Saenz says.
The concept is still very much in the laboratory phase, but if all goes well, robots would be phased in gradually, ‘No one is suddenly going to lose their jobs, explains Mr Saenz. On the contrary, the robots would allow people to stay in work longer, handling the physically stressful or very repetitive tasks, ‘Expertise and know-how can be more highly valued, he adds.
The project is getting direct input from the floor of the Airbus and Austrian FACC factory (two of the partners in the project) as people say what tasks they would like their metal co-workers to handle. ‘If robots are hard to set up or monitor, people will always prefer to quickly step in and do the task themselves, Mr Saenz adds. ‘We dont want to be creating costly machines that then end up in the corner gathering dust. We want to make robots that will work alongside humans, doing the things humans dont want to do, to free up the people to do the brain work.
http://cordis.europa.eu
Featured Product
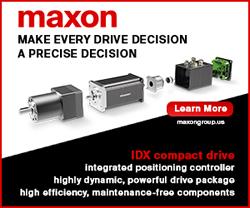
The maxon IDX Compact Drive with Integrated Positioning Controller
The compact brushless EC-i motor combined with an EPOS4 positioning controller delivers a highly dynamic, powerful drive package with field-oriented control (FOC), high efficiency, and maintenance-free components in a high-quality industrial housing. The maxon IDX drives are suitable for use across the entire speed range (from standstill to maximum speed) and have an extremely high overload capability. Together with a positioning controller, the integrated sensor (single turn) enables absolute positioning.