Lightweight, Soft Exosuit Aims to Prevent Musculoskeletal Injury in Warfighters
Suit conforms to the body, allowing for natural joint movement while augmenting effectiveness
Harvard Universitys Wyss Institute for Biologically Inspired Engineering is continuing development of a lightweight, soft exosuit for DARPAs Warrior Web program, which is aimed at creating technologies that mitigate musculoskeletal injuries among warfighters while improving performance. The Wyss team is seeking to integrate component technologies developed in separate Warrior Web efforts into a prototype suit that offers expanded capabilities. DARPA plans to test the final suit in appropriate mission profiles under realistic loads to evaluate performance.
The equipment and gear carried by todays dismounted warfighter can exceed 100 pounds. This added weight—especially while bending, running, squatting, jumping, and crawling in a tactical environment—increases the risk of musculoskeletal injury, particularly in such areas as ankles, knees, and lumbar spine. This load weight also causes increase in physical fatigue, which further decreases the bodys ability to perform and protect against both acute and chronic injury.
The Warrior Web programs ultimate goal is a lightweight, conformal under-suit that is functionally transparent to the user—similar to a divers wetsuit. As envisioned, the suit will ultimately employ a system of closed-loop controlled actuation, transmission, and functional structures that protect injury prone areas, focusing on the soft tissues that connect and interface with the skeletal system.
The current Wyss Institute suit is made of soft, functional textiles woven into a piece of smart clothing that is pulled on like a pair of pants and intended to be worn under a soldier's regular gear. Through a biologically inspired design, the suit mimics the action of the leg muscles and tendons when a person walks, and provides small but carefully timed assistance at the joints of the leg without restricting the wearer's movement. For a demonstration, see: http://vimeo.com/100446428.
Featured Product
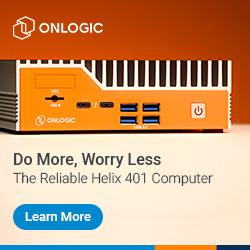