Morgan Advanced Materials announces advances in their range of high purity materials for semiconductor applications
Morgans CVD Silicon Carbide (SiC) and Pyrolytic Boron Nitride (PBN) materials are ideal for use in semiconductor applications
Morgan Advanced Materials announces advances in their range of materials grown using chemical vapor deposition (CVD) processes. Morgans CVD Silicon Carbide (SiC) and Pyrolytic Boron Nitride (PBN) materials are ideal for use in semiconductor applications, including rapid thermal processing and plasma etch process chamber components, as well as metalorganic CVD tools for high-brightness white LED manufacturing using the indium gallium nitride process.
Morgans improved CVD SiC growth capability enables the manufacture of 300+ millimeter diameter components with thicknesses of more than 10mm at production volumes for recently developed plasma etch applications. With access to world class ultrasonic machining capability, Morgan offers high tolerance CNC machining and precision hard grinding, as well as the patented Rmax process for producing focus CVD SiC ring shapes.
Morgans high purity (99.999 percent+) SiC material has high thermal conductivity, is resistant to chemical erosion, and features minimal particulate generation, making it ideal for use in chlorine and fluorine plasma etch processes. The material is ideally suited for use in producing GDMs (gas distribution plates) where the materials erosion resistance can lead to long life and extended tool PM schedules. Ultrasonic drilling can provide holes with diameters as small as 0.5mm, ideal for custom etch applications.
High purity (99.99 percent+) PBN materials have a working temperature in excess of 1500°C, and feature high electrical resistivity and high dielectric strength. Extremely low out-gassing, non-wetting, and non-toxic, the PBN materials are inert to most acids, alkalis and organic solvents and have high thermal conductivity in the "a" direction. The advanced materials are a good choice for manufacturers of PBN coated graphite heaters and PBN effusion cell components.
For more information about our range of CVD materials please visit http://www.mtccvdmaterials.com/cvd.
Featured Product
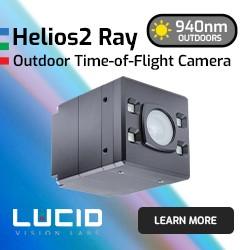