Schunk - Standardized RCC axes for high-speed assembly
The linear modules of SCHUNK's LCx series set a new benchmark.
When complete Z or Y axes are to be moved in high-precision high-speed applications, the linear modules of SCHUNK's LCx series set a new benchmark. The profiles of the world's first standardized linear motor axes made of reinforced carbon composite weigh approximately 58% less than the profiles of comparable aluminum modules resulting in quicker acceleration with less energy. Since the thermal expansion of the material is minimal, the axes ensure high precision even when they heat up during operation.
Light-weight modules in the LCx series result in high speed and accurate repeatability due to a servo-electric linear motor drive. The driving force is transmitted by high-precision drive elements, directly to the slide while precision-cut steel guide rails increase accuracy. The absolute-value transducers provide excellent repeat accuracy of 0.01 mm per axis and eliminate the need for expensive homing when the system boots and after emergency stops.
Since the motor, measuring system, and linear guidance are integrated directly into the axis profile, the modules are extremely compact and require very little space. Additionally, multiple freely programmable slides on a profile guide enable compact and affordable concepts. For use as a Z-axis, a parking brake may optionally be added to the modules.
The standardized carbon axes come in two versions: one is the LCN version with a simple X profile, in which the axis reaches a rated force of 200 N and a maximum driving force of 500 N. The other is the LCM module, which is designed for moderate loads, is equipped with a wide double X profile, and achieves a rated force of 400 N and a maximum driving force of 1,000 N. In both versions, the maximum acceleration is 40 m/s2, the maximum speed is 4 m/s1, and the maximum useful stroke is 1,200 mm.
The modules can be used both horizontally and vertically, optionally with a static profile, and moving slide or with a static motor and moving profile. The axes are controlled with Bosch Rexroth IndraDrive controllers as standard; a Siemens SINAMICS S120 drive is also possible as an option. Because SCHUNK offers all LDx modules with the standard interfaces Profibus, Sercos III, Profinet IO, EtherNet/IP and EtherCat, the modules can be quickly and easily integrated into higher-level system controllers.
About SCHUNK:
SCHUNK is the worldwide competence leader for clamping technology and gripping systems. Totaling more than 60 years of experience, SCHUNK is a family owned operation and a global player in one. For more information, visit www.schunk.com
Featured Product
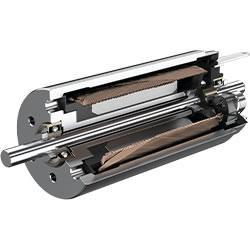