Harper Partners with University of Colorado Boulder to Engineer Cutting-Edge R&D System for Advanced Magnesium Processing
One of the most advanced customizations of the Harper system includes the hybrid utilization of both electric energy and renewable, concentrated solar power for heating.
Buffalo, NY - Harper International, world leader in thermal processing solutions for advanced materials, has finalized a contract for a research scale high-temperature reactor to support University of Colorado Boulders development of magnesium for lightweight vehicle parts. CU-Boulder was awarded a three-year, $3.6 million grant from the U.S. Energy Departments Advanced Research Projects Agency in September of 2013. CU-Boulder Professor Alan Weimer and his research team will utilize the Harper reactor to produce both magnesium and synthesis gas, or syngas, a precursor for synthetic gasoline.
Harpers unique system will perform the advanced carbothermal reaction of carbon and magnesium oxide, which are heated to high temperatures to produce magnesium vapor and carbon monoxide gas. While the magnesium vapor is converted into a solid metal, the carbon monoxide is combined with steam and excess heat recovered from the solar-electrical reactor to shift the carbon monoxide into hydrogen and carbon monoxide, the syngas building blocks that can be catalytically reacted into diesel fuel or gasoline.
One of the most advanced customizations of the Harper system includes the hybrid utilization of both electric energy and renewable, concentrated solar power for heating. The current leading process to produce magnesium involves using electricity 24 hours a day, a method that is particularly expensive because of high-energy consumption during daylight hours. The CU-Boulder team will use solar energy to power the reactor in the daytime and use electricity only at night during off-peak hours.
"Harpers custom system will enable us to not only make magnesium, a high value and strategic material, but also to make fuel, and in a more energy-efficient manner," said Professor Weimer. "Our partnership with Harper throughout the design process yielded a one-of-a-kind hybrid solar/electric cavity reactor that will propel our critical research for producing magnesium as well as future materials."
Magnesium is 75 percent lighter than steel and 33 percent lighter than aluminum. By 2020, magnesium parts will allow cars and trucks to weigh 15 percent less, leading to fuel savings of 9 to 12 percent, according to the U.S. Automotive Materials Partnership, an industrial coalition of the Chrysler Group LLC, the Ford Motor Company and the General Motors Co. The Weimer research lab has been engaged in solar-thermal processing for the past 17 years and is the largest academic solar-thermal chemistry research team in the United States.
About Harper International
Harper International is a global leader in complete thermal processing solutions and technical services essential for the production of advanced materials. From concept to commercialization, from research scale to full production line operations, Harper is perpetually on the cutting edge of the most innovative furnace and oven designs in the world. For decades, we have pioneered some of the most unique, customized systems available, with a focus on processing materials at high temperatures up to 3000°C and in non-ambient atmospheres. For additional information, please visit www.harperintl.com or email info@harperintl.com.
Featured Product
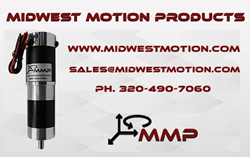