Darpa - MINIMIZING UNCERTAINTY IN DESIGNING COMPLEX MILITARY SYSTEMS
DARPA program seeks novel mathematical research for quantifying and predicting uncertainty in design models as alternative to costly and repetitive testing
Uncertainty is sometimes unavoidable. But in the world of scientific computing and engineering, at least, whats worse than uncertainty is being uncertain about how uncertain one is.
Understanding with confidence the level of uncertainty in computational models used for designing complex military systems—such as new aerospace vehicles and engines, for example—can be enormously beneficial, reducing costs and development times. But achieving a useful degree of such confidence is a difficult mathematical challenge, given the large number of variables typically involved. As a result, engineers have come to rely on extensive testing to verify their modeling results—a repetitive process of design, test, verify, re-design, re-test, re-verify that can add years to the development process.
DARPAs Enabling Quantification of Uncertainty in Physical Systems (EQUiPS) program aims to solve this problem by developing the mathematical tools and methods to efficiently quantify, propagate and manage multiple sources of uncertainty. The goal is to create a computationally effective and mathematically rigorous framework for engineering that will accurately predict, on the basis of complex design specifications, the functional operation of complex defense-related physical and engineering systems. For example, one might want to predict the performance of an airfoil (or even design an airfoil from first principles) given known uncertainties in angle of attack, air speed, environmental conditions and design imperfections - without having to resort to extensive and repetitive testing.
"In recent decades, the field of uncertainty quantification has made significant progress dealing with what is known as the ‘forward problem, which refers to propagating input uncertainties through a computational model," said Fariba Fahroo, DARPA program manager. "These methodologies can now handle forward problems for a small number of uncertain parameters, but they still cant handle more complex, extremely high-dimensional industrial physical systems and they do not directly address the challenges of uncertainty quantification in inverse problems, including uncertainty in the models themselves. Dealing with the ‘curse of dimensionality where the associated computational cost grows exponentially as a function of the number of random variables remains a major challenge in simulation and design under uncertainty."
DARPAs Broad Agency Announcement solicitation with more details on the EQUiPS program is available here: http://go.usa.gov/eZUC. Abstracts are due by 4:00 p.m. EST on Jan. 15, 2015. Full proposals are due by 4:00 p.m. EST Feb. 25, 2015.
Featured Product
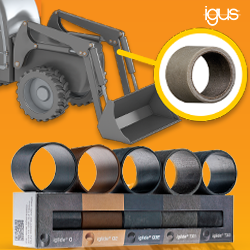
igus® - Free heavy-duty plastic bearings sample box
The iglide® heavy-duty sample box provides a selection of five unique iglide bearings, each suitable for use in heavy-duty equipment due to their self-lubricating, dirt-resistant properties. Each bearing material boasts unique benefits and is best suited for different application conditions, though each can withstand surface pressures of at least 11,603 psi at 68°F.